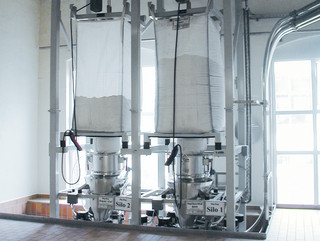
Use available storage space effectively
Space is a consistent concern in any manufacturing plant. Indoor warehouse space is expensive and is usually in short supply. In addition to spatial concerns, concern for storage climate is also important. Ideally storage space for ingredients should be climate-controlled for protection from both excessive heat and cold. If recent temperature extremes seen in Texas or Florida are any indication, manufacturers cannot be too careful when it comes to protecting their materials from exposure to the elements.
On a similar note, ingredient security is also a factor. Regardless of where bagged materials are in a facility, they need to be safe from contamination, pests or deterioration. Whether looking to prevent material from going rancid, clumping or bricking if the product gets too humid, your bags and super sacks need to be up to the task. Stock should be rotated regularly, with particular attention paid to ensuring oldest products are used first, as well as keeping a close eye on potential pest infestation.
Another consideration is physical distance between the warehouse and manufacturing. Ingredients are always needed during production hours, which can tie up both labor and equipment if storage and production are not close together.
Store super sacks so you access them
At the risk of understatement, ease of access is the most important factor when storing bagged materials. Super sacks have to be moved by forklift, so aisleways need to be wide enough for both the forklift and the bag. Particular care should be taken to ensure that sacks are not punctured or otherwise damaged while being moved in and out of storage.
Storing super sacks on racks allows you to optimize available vertical space. Attaching super sack “straps” to the forklift requires manual assistance, so super sacks stored in racks above the floor should be stored on pallets to facilitate access.
Floor storage is cheaper than rack storage – rack systems can be very expensive to install – but it can waste vertical space above the pile. Floor storage is best when pyramid stacking can be done, or with supported stacking when the pile is supported by walls on two sides.
Piles are suitable for most bagged ingredients, but those that are susceptible to environmental issues, temperature, humidity or pests, must be accessible. Access for proper stock rotation is important – bags in the back or on the lowest level of the stack are prone to spoilage or expiration. Out of sight, out of mind.
Look for the following to ensure quality sacks
Super sacks, officially known as flexible intermediate bulk containers (FIBC), have quality standards governed by ISO-21898.
Super sack FIBCs should be labeled with the following:
- Manufacturer name and address
- Manufacturer’s reference number
- FIBC class (one-time or multiple use)
- Safe working load (with unit of measure) safety factor
If unsure, TEN-E Packaging Services in North Carolina provides independent verification and testing services.
Broken bags should be treated with special attention. A floor-level bag with a large tear could jeopardize the stability of stacked bags above it and the safety of nearby workers. Start by taking bags off the top and work your way down to the broken bag.
Ultimately, super stack storage boils down to stack or rack? The answer to that question will come down to a handful of other key questions:
- What is in the bag?
- Is it ok to sit the bag on the floor?
- Is your super sack properly labeled?
- Are your bags strong enough to stack?
Only after these basics have been addressed can you optimize your super sack storage.
If you're considering investing in a super sack unloading system or have any questions on how to help your plant and processes run smoothly in general, feel free to contact our AZO sales team. AZO has more than seven decades of experience in handling raw materials and shaping ingredient automation along the way.