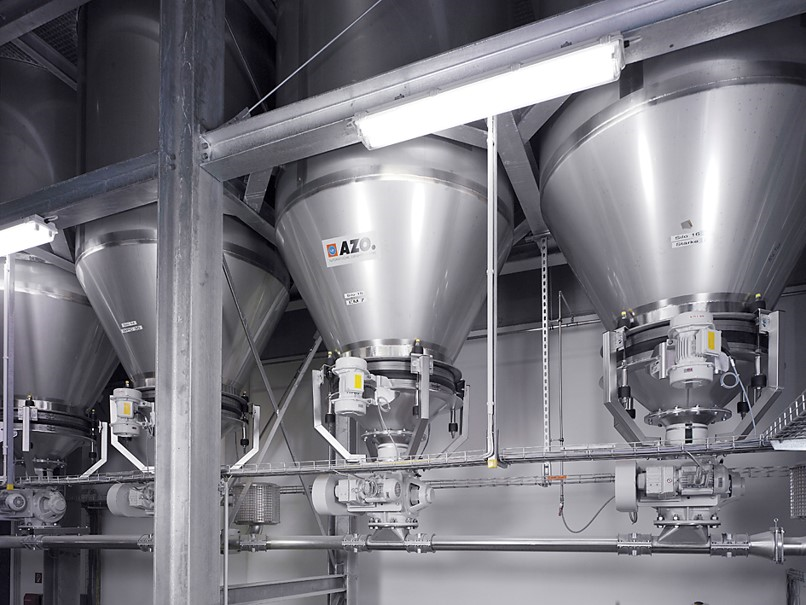
How to plan for hidden costs during the startup, maintenance or operation of a conveying system is often difficult to pin down. That’s why we’ve sorted through some common hidden costs related to conveying systems that can become major concerns for any plant manager looking to properly set up, maintain or operate these systems.
The pickup point of a dilute phase vacuum system
We’ve already covered the hidden costs of a system startup in blog form, and our free conveying guide contains a wealth of information related to pneumatic conveying in the process material handling world. For your convenience, we’ve also zeroed-in on some pertinent common hidden costs of conveying operation here.
Not having a well-established and proactive maintenance plan
A well-established and proactive maintenance plan can catch and fix potential problems before they occur. Otherwise, you are essentially waiting for something to fail, which will lead to costly downtime and higher repair costs. Proactive system maintenance will pay for itself with improved system reliability.
Lack of operator training
Lack of operator training can lead to bad batches and therefore, wasted product. Wasted product essentially means lost money. Something as simple as someone forgetting to flip a switch can be a result of improper training.
Another example could be forgetting to turn the compressed air back on and the filter getting backwash from the receiver. The conveying line then becomes plugged because the filter is plugged, and the convey air fills the receiver. Air then stops flowing. Proper training could have prepared this operator to do suitable and correct system maintenance.
Leaks in the system
Just as air leaks in a conveying system are a typically overlooked cost during system startups, during operation they can significantly reduce system efficiency. Blowers will run longer and work harder to move the extra air brought in by leaks in the conveying lines. In pressure systems, leaks will lead to waste as ingredients escape the conveying lines and enter the atmosphere creating a potential dust hazard. Checking for leaks is sometimes difficult to do. For example, it seems most of the valves in a conveying system are located 30 feet in the air. It takes a substantial amount of time and effort to retrieve a lift and get a mechanic into position to fix some leaks, but the effort is worth the efficiency gains.
The destination point of a dense phase vacuum conveying system
As a side note: Leaks in vacuum systems are harder to find because when you’re pulling a vacuum, you can’t see the air entering the pipe. This is as opposed to a pressure system where you can visibly spot the powder blowing out of the leak and exiting the system.
Inadequate compressed air supply
If there’s inadequate compressed air supply, many mechanisms in a conveying system don’t function properly. This is because compressed air is an important utility that’s required to make many parts of a system function.
For instance, to open and close a valve on the bottom of a weigh hopper (where material is held before it is dumped into a mixer), requires compressed air to activate the valve. You also need to have compressed air to clean the filters in the receiving hoppers at the end of the conveying lines. Adequate air supply is critical for successful system operation.
Lack of spare parts inventory
Production downtime is wasted money in any production facility. From minutes to hours, management will equate any amount of downtime to lost production time. Not having spare parts on hand for critical items can truly be an unexpected disaster that could seriously compromise system operations. AZO is always willing and able to help you acquire the spare parts you need as soon as possible, but any time spent waiting on these spare parts to arrive is lost time that should be spent making saleable product.
It’s best to plan ahead and have spare parts on hand before an unexpected incident or failure in your process occurs. This way you minimize downtime and prevent long-term production hiccups due to not having a critical spare part close at hand.
If you have any questions about spare parts, pneumatic conveying systems or material handling in general, don’t hesitate to contact an AZO sales representative. AZO developed the original cyclone screener in 1949, and we haven’t stopped innovating the ingredient automation industry since. Read more of our blog to find information on pneumatic conveying, ingredient automation and the reliably accurate equipment that AZO manufactures. As mentioned, our free conveying guide covers many topics related to pneumatic conveying and material handling.