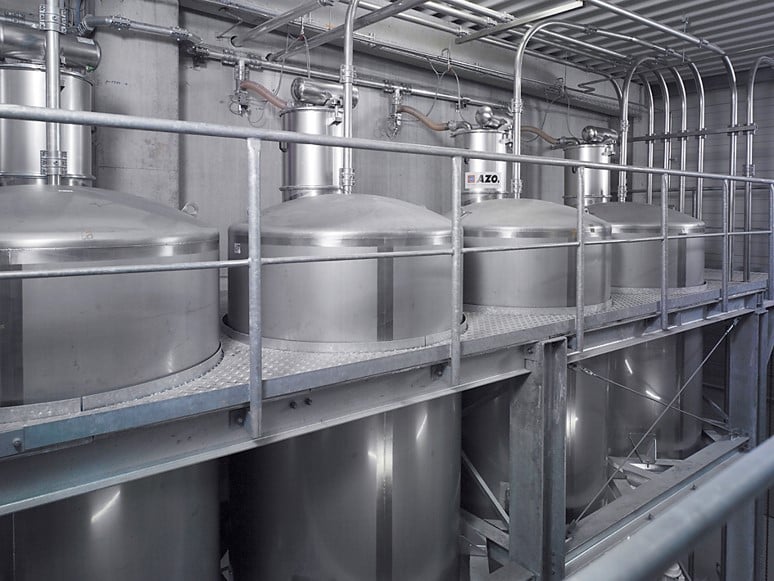
In our previous discussion on optimizing bulk ingredient handling systems, we explored how proactive service and maintenance play a critical role in improving operational efficiency. That first round of optimizations delivered significant improvements, stabilizing system performance at 79% efficiency. But what happens next? Can a system go beyond 100% efficiency, and if so, how?
This follow-up dives into new challenges, key system adjustments, and the strategies that pushed the system beyond full capacity—reaching 102% efficiency.
From Optimization to Peak Performance
The initial optimization process focused on discharge efficiency, pump performance, and material flow consistency. After these adjustments:
- The plant was running at 79% efficiency.
- Optimization efforts targeted performance consistency across all lines.Further fine-tuning on the six mix lines ensured stable operation.
By the time of the follow-up assessment, system settings had remained unchanged—a good indication that the initial optimizations created a strong foundation for efficiency. However, a new set of challenges emerged.
Addressing Unexpected Challenges: The Case of Silo 11
One major issue discovered during follow-up visits involved Silo 11, which handles leon-lite —a fine, powdery ingredient used in production.
The Problem: Dusting from Pressure Relief Valves
- The fine product was escaping through the pressure relief valves (PBR valves), causing severe dusting on the upper floors.
- Employees could see visible dust clouds, signaling poor containment and ingredient loss.
- Instead of addressing the issue, the plant had allowed the dusting to continue, impacting air quality and safety.
The Solution: Optimizing Filtration & Airflow
The investigation revealed that compressed air settings and filter sequences had been altered. The fix involved:
- Upgrading the Filtration System
- Replaced standard filter bags with Teflon-coated PFD bags for better containment.
- Adjusted the filter cleaning sequence and pressure settings to improve filtration.
- Optimizing Airflow
- Increased compressed air pressure to maintain proper dust control.
Immediate Impact
- Dusting was completely eliminated, improving workplace conditions and reducing material loss.
- Ingredient containment improved, ensuring proper usage of raw materials.
This case reinforces a key lesson: seemingly small inefficiencies—like altered air pressure settings—can create major operational disruptions if not addressed promptly.
Reaching 102% Capacity: How It Was Achieved
With the dusting issue resolved, the next goal was to push system efficiency to its maximum potential. The adjustments that made this possible were precise and data-driven.
Key Adjustments for Full Optimization
- Pressure relief valves on pumps were adjusted to 550 millibar, providing 16.24inches of mercury.
- High vacuum settings were increased from 13.5 inches to 14 inches, improving conveyance power.
- Material transfer rates were optimized, allowing the system to operate at 13 inches of mercury instead of 12.
Results: Exceeding Expectations
- These refinements unlocked additional system capacity, pushing efficiency to 102%.
- The system not only met, but exceeded, expected performance levels, proving that incremental fine-tuning can lead to substantial efficiency gains.
Customer Benefits: What These Changes Mean in Practice
Beyond the numbers, these optimizations created tangible benefits for the plant.
Increased Production Speed
- Previously, the mix tower struggled to keep up with packaging.
- Now, the mix tower runs ahead of packaging, shifting the bottleneck to the next phase of production.
Cost Savings & Waste Reduction
- Ingredient loss due to dusting was eliminated, leading to significant material savings.
- Enhanced vacuum and filtration settings reduced maintenance costs and prolonged equipment lifespan.
Long-Term System Stability
- The plant now operates at a consistent, high-efficiency rate.
- Even after months of operation, settings remained stable, confirming the sustainability of these improvements.
Sustaining Peak Efficiency: Recommended Long-Term Strategies
Optimization doesn’t end when efficiency improves—it requires ongoing monitoring and proactive service.
Designating a Dedicated Technician
- A plant maintenance worker was trained as an in-house AZO technician to oversee system performance.
- This ensures real-time troubleshooting and immediate adjustments, reducing dependency on external service calls.
Implementing Annual System Reviews
A yearly AZO technician visit was recommended to:
- Assess equipment health
- Verify discharge rates
- Fine-tune system settings to maintain peak performance
Continuous Performance Tracking
- Regular data logging ensures early detection of potential inefficiencies.
- Proactive tracking allows adjustments before small issues turn into major performance losses.
Next Steps: Engineering Studies & Future Upgrades
Following the success of these optimizations, the company is now conducting an engineering study to explore additional system upgrades, including:
- Advanced automation solutions to further enhance efficiency.
- New ingredient handling systems to accommodate increased production demands.
- Real-time performance analytics for predictive maintenance and continuous optimization.
By focusing on ongoing system improvements, the plant can maintain its competitive edge and operational efficiency.
Why Service Matters
This optimization journey—from 79% efficiency to exceeding 100% capacity—demonstrates the power of proactive system improvements. Regular service, precise tuning, and strategic oversight can transform a system from functional to exceptional.
For bulk ingredient handling systems, the key to success lies in ongoing maintenance, smart automation, and leveraging expert support. The lessons from this project reinforce the value of working closely with experienced service providers to achieve peak performance and long-term efficiency.
Looking to optimize your system further? Explore how AZO’s service and engineering solutions can help you unlock new levels of efficiency and reliability. Contact us today.