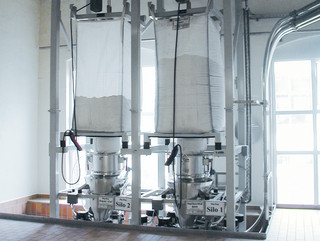
Make Your Bulk Material Handling Process Easier
You have your big bag unloader, and you’re ready to take your bulk material handling process to the next level. But you quickly realize there is a lot that has to happen during discharge. And now you’re wondering if you need options.
This simple question opens up an important conversation around optimizing this first step in your bulk material handling. It also highlights an interesting difference in how people buy this "component" that's perceived as simple, versus a more complex factory-wide solution.
Bulk bag unloaders are often sold as stand-alone components. In some ways they’re simple, almost hot-swappable, pieces of hardware. It’s just a metal frame holding a bag while material flows out. That's certainly less complex than pneumatic conveying, blending, weighing, mixing and bulk packaging. But it's not necessarily simple.
Not only are there substantial differences in safety (e.g. electric hoist vs. fork truck), and regulatory requirements that vary by industry (e.g. closed profile construction) but the product itself adds to the complexity of the design challenge in many cases.
Optimizing flow is critical to successful bulk bag unloading — and since this is the first step in a bulk material handling system, it's key to the overall success, too.
Go with the Flow to Start
A product’s flow often depends on two things: the nature of the product and environmental considerations. Further, ease of starting the flow is not necessarily indicative of ease of keeping product flowing once it's started. If only all products were as simple as common polyethylene resin pellets, which tend to be free flowing and easy to keep moving!
Your product is likely more complex, and if you're accustomed to working with 50-pound bags, it will likely behave differently in a bulk bag just as it will vary from batch to batch — much less from one vendor to another.
While free flowing products like granular sugar or silica powder are often easy to get moving, they may be more susceptible to bridging, ratholing and other common flow challenges. In contrast, products which are quite cohesive and/or adhesive like TiO2 or high-fat-content ingredients, like milk powder, will likely require more mechanical assistance to get them moving.
Even products that flow smoothly require assistance to ensure that bags are completely emptied.
Preparing Product to Flow
Sometimes consistent flow begins even before the bulk bag is loaded into the unloader. If you run products for pharmaceutical, food or process applications that preclude the addition of flow agents to bulk materials, then you've probably experimented with "hickory conditioning."
Never called it by that name? That's fine, but you've probably observed the process. Often blocked product in bulk bags are literally beaten with baseball bats for up to an hour to break the material into small enough pieces to flow through the 16-inch diameter outlet spout.
Not only is that time consuming and labor intensive, but there are obvious operational and safety considerations. There is, however, an automated, safer and more consistent solution. A bulk bag deblocker uses hydraulic arms to pressure the bag from all sides to break what might be a 2,000-pound slug of material into pieces small enough to flow out.
A delumper machine is another option. It's often used in conjunction with a deblocker or independently for product that clumps but doesn't block. A delumper machine, typically a rotating mechanical device, takes product flowing through the outlet spout (up to 16-inch diameter) and breaks it into small flowable products of 1/4-inch diameter or less.
Mechanical Options to Assist Flow
Even the easiest and most consistently flowing products typically require some mechanical assistance to optimize the operation.
The most common solutions are massage pads, vibration, and elongation.
Massage Pads
Massage pads are used to deform the bag. This can help move product toward the center by changing the angle of flow. This common option is available in various configurations from most manufacturers. It's important to evaluate the specific mechanical execution from a safety perspective, however, since many introduce pinch points. (For more considerations when buying a bulk bag unloader, check out our free downloadable buying guide.)
Mechanical Vibration
Mechanical vibration is a simple and widely used addition to bulk bag unloaders. A motor, often with unbalanced weights, provides vibration of the bag from below. AZO's vibration is actually transmitted to the bag through the full safety tray on which the bag sits (and which protects workers from potential injury from a falling bag while working on connecting the discharge spout).
Bag Elongation
As a bulk bag is emptied, the shape changes and product is more likely to gather in the corners at the bottom and folds. Elongating the bag by pulling the top up is a simple step that's commonly used to facilitate flow as a bag nears empty.
Managing that with a fork truck loaded system, however, can create safety issues, and it's not necessarily simple to execute. In contrast, a bulk bag unloader that's equipped with an electric hoist, supports quick and convenient bag elongation to encourage full discharge of bulk material that might otherwise stay in the bag and then create housekeeping and safety issues with dust as it's collapsed.
Don't Underestimate the Complexity of a Bulk Bag Unloader
Compared to an entire system, the bag unloader is a simple piece. But assuming that it should be ordered as a standard, MRO item is likely to lead to problems. Don't overlook common options which are important to improve operations. These should be evaluated in the context of your specific current and projected product, operations and environmental considerations.
Spending a bit of time with a capable sales engineer at the project outset will help to ensure that you're buying more than just a sturdy steel frame.
Need a drawing and quote in a hurry? Our configurator can help. Answer a couple questions and we can provide immediate answers for many common applications.