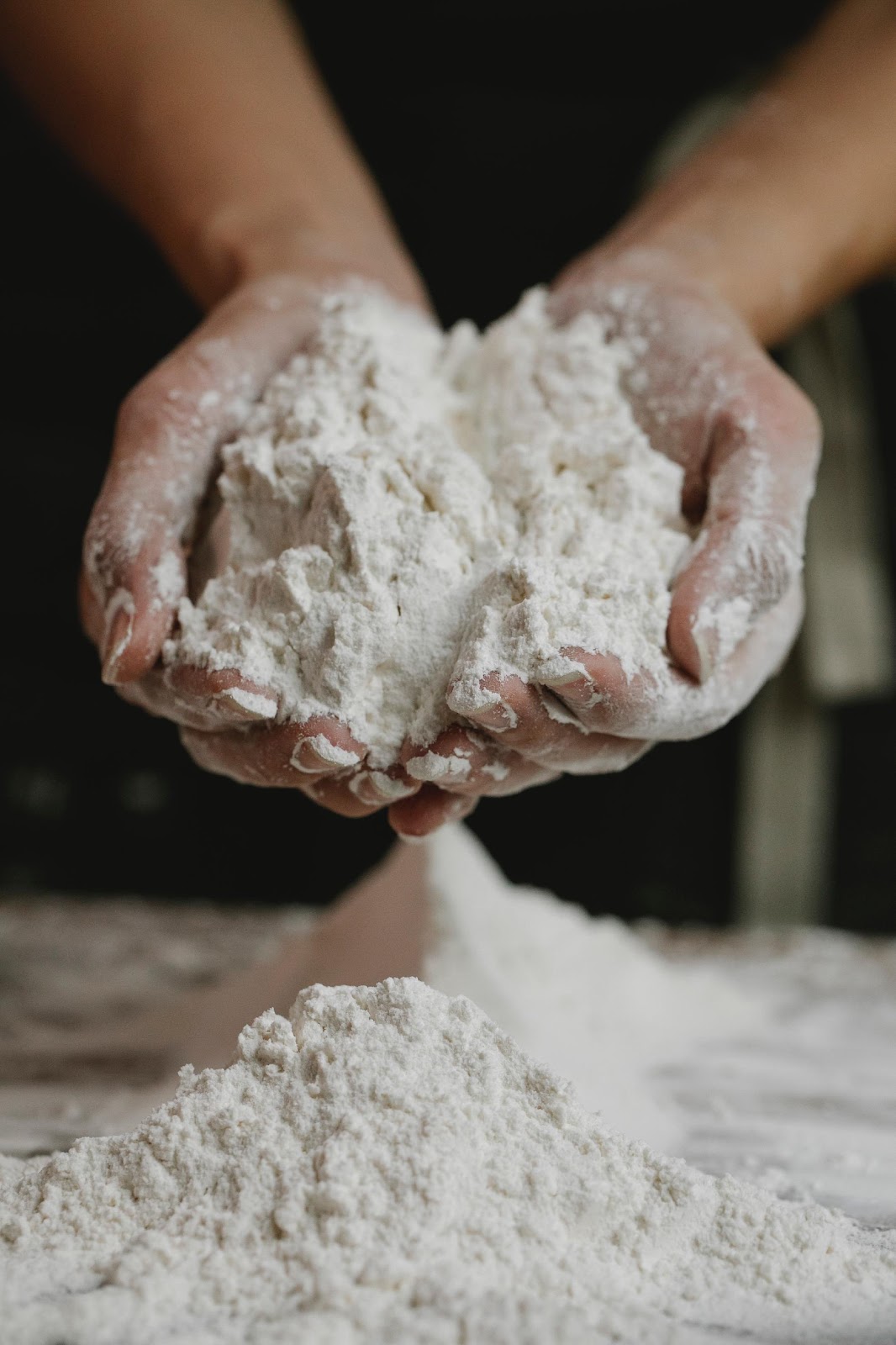
In the world of bulk material handling, it is understood that different materials possess different characteristics. This comes into play when product flow is concerned because some materials are free-flowing and do not require any extra design efforts. Other materials are severely resistant to flow.
In order to help manufacturers in understanding their material behavior more effectively, we’ve put together a list of specific terms relating to bulk material characteristics. We’ll also share important info related to material testing toward the end of this blog post, but what immediately follows are critical terms for use when describing various materials that are handled in bulk.
Cohesion and adhesion represent how likely a material might stick to itself or to stick to the surface of the vessel.
Aeration pads from AZO
Aeration is the practice of adding a prescribed amount of air to material in order to make that material more fluid. Certain types of material actually densify with vibration. Examples of materials with this characteristic include diatomaceous earth, cocoa powder or carbon black. Aeration pads contain openings that allow for air to be pushed through them. Air moves to the material, effectively altering the bulk density of the material for a given time.
Compressibility represents how much material will naturally compact. Over time, the weight of material alone will cause it to compress at the bottom of a large silo. This can reach a point where the material is compressed so much that it will not discharge.
Wall friction is the resistance to flow between the materials and the hopper wall surface.
Tapped density is a term that represents how much a material will actually compress.
Shear represents how much force molecules of a given material can take before it will give way and start sliding across a surface or against itself. When a shear test is done on a material, force is applied to determine that material’s limit.
A common misconception is that the angle of repose will directly determine the vessel cone angle. These two factors actually have not much to do with one another. The angle of repose is used to determine how much material can be stored in a vessel by taking the conical pile at the top of the material as it collects in a vessel. This helps to understand the total volume. Angle of repose also gives a clue as to a material’s ability to be free-flowing vs. non-free-flowing.
Material testing is important but so is referencing past experience
While different kinds of material tests are specifically and individually important, the results of past tests an equipment manufacturer has performed helps to gain an understanding of how to interact with a customer's ingredient or material going forward.
Specific results can be determined through lab tests at the Thorp Callaway Ingredient Automation Test Facility located in Memphis, TN. Here at this in-house lab, AZO technicians can properly assess if material can be successfully handled in a pneumatic conveying system.
Many manufacturers think that conducting various tests is the surefire way to determine what type of storage vessel should be implemented. Still, while the data points collected from different tests are useful, there generally isn’t one simple way to determine the most appropriate details concerning vessel geometry and cone angles. This is because there are many variables within each one of these tests, and each test has an appreciable effect on the next. It becomes difficult to ascertain precise conclusions based on these different variables.
Instead, equipment manufacturers often consider examining materials based on reference to previously tested materials. Past experience, in conjunction with lab testing, is the great determinant for what should be done with an application. At AZO, we examine materials by a “class” basis including “free-flowing,” “moderately free-flowing,” “poor flowing,” or simply “non-flowing” material.
A new, free guide from AZO further elaborates on various mechanical devices that are used to apply energy into material in order to induce flow. “Flow and Functionality: Determining The Proper Discharge Aids For Your Bulk Material Handling Process” contains pertinent information about many machines that are often used in concert with each other (as well as flow agents) to overcome the friction between material and the wall of storage vessels.
If you find that you have any other conveying queries, you can always feel free to speak to an AZO specialist. We have more than seven decades of experience in handling raw materials and shaping ingredient automation along the way. Contact our sales team for any questions on how to help your plant and processes run smoothly.