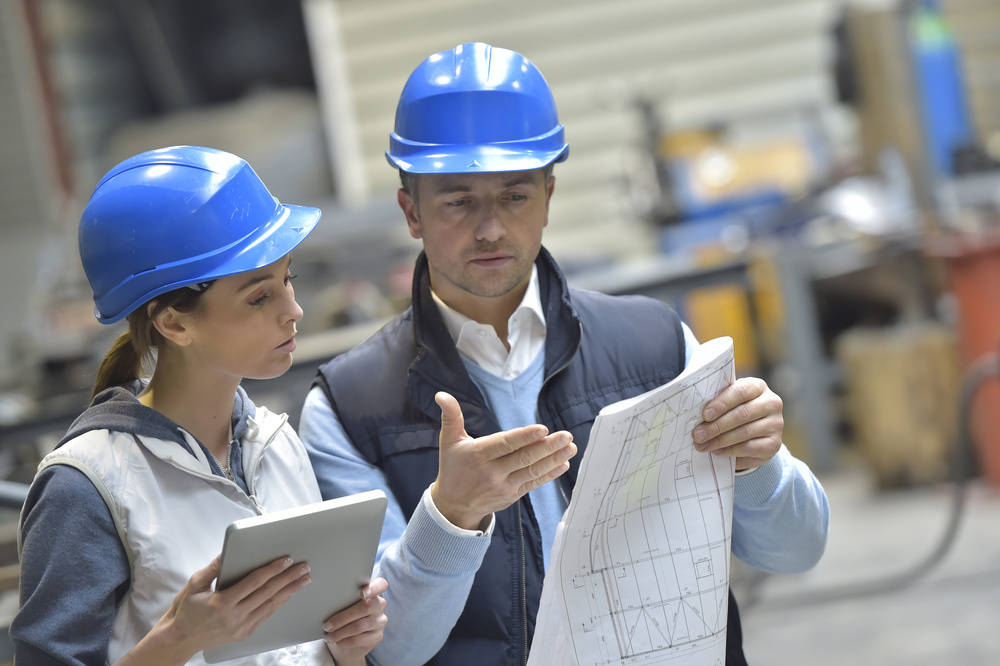
The cost of downtime in manufacturing goes beyond lost revenue—it can damage trust and throw off schedules. A proactive approach to spare parts management is essential to keeping your systems running without a hitch. Let’s break down how it works.
Identifying Critical Components for Your Pneumatic Vacuum Systems
Some components are more prone to wear and tear than others. Identifying these critical components is the first step toward effective spare parts management. Focus on essential parts such as vacuum pumps, filters, valves, seals and gaskets, pneumatic actuators, and hoses and fittings. These are high-risk failure points due to continuous use, contamination, or pressure changes.
By prioritizing these components, you can create a targeted spare parts inventory that ensures the system remains operational with minimal downtime.
Organizing and Categorizing Your Spare Parts Inventory
Efficient organization and categorization of your spare parts inventory can significantly reduce downtime. Start by classifying parts into high-priority (critical to system operation) and low-priority (non-essential but good to have). You can further group parts based on their usage frequency—frequently replaced parts like filters and seals should be easily accessible.
Using labeled bins or shelving can simplify the identification process, allowing for quick retrieval during maintenance or emergency repairs. Ensuring that your storage system is orderly and intuitive will save valuable time and effort.
Aligning Spare Parts with Maintenance Schedules for Optimal Performance
Aligning your spare parts inventory with maintenance schedules is crucial for optimal system performance. Preventive maintenance involves scheduling regular part replacements to avoid emergency repairs, while predictive maintenance uses monitoring tools to anticipate part replacements based on system performance data.
By planning part replacements during scheduled downtime, you can minimize disruption and ensure that your pneumatic vacuum system operates smoothly. This proactive approach helps in managing spare parts more efficiently and reduces the risk of unexpected breakdowns.
Building Strong Supplier Relationships for Reliable Part Availability
Reliable supplier relationships are vital for ensuring the availability of high-quality spare parts. Work with trusted vendors who understand the specific needs of pneumatic vacuum systems. This includes having suppliers who can provide expedited shipping for urgent requirements.
Balancing the use of OEM parts for critical applications and aftermarket parts for non-critical components can also help in cost management. A strong supplier network can significantly reduce lead times and ensure that you always have the necessary parts on hand.
Monitoring System Performance and Optimizing Spare Part Costs
Monitoring system performance is essential for optimizing spare part costs. Real-time data from sensors monitoring vacuum levels, airflow, and pressure can detect early signs of component wear. Keeping records of part lifespans and analyzing failures can help in predicting replacements and preventing repeat issues.
Cost optimization also involves strategies like bulk purchasing of high-usage parts, considering refurbished components for less critical applications, and avoiding overstocking. Regularly assessing your inventory can prevent the accumulation of slow-moving or obsolete parts, ensuring efficient use of resources.