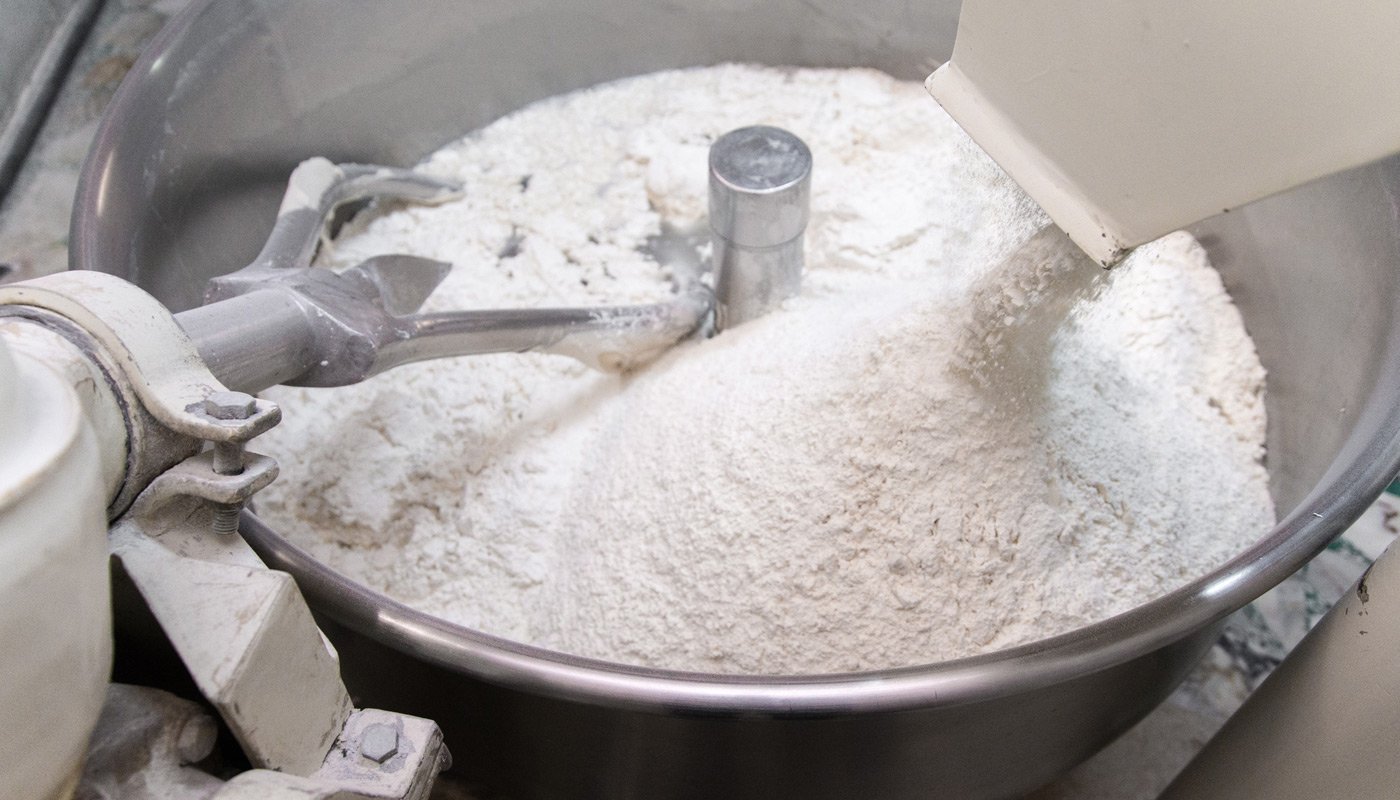
In the realm of dry powder mix manufacturing, precision and consistency are the cornerstones of success. One company, which we'll refer to as the "Dry Mix Innovators," specializes in creating dry mixes for the consumer market. Their recent endeavor to switch from granular sugar to maltodextrin in their mixes came with unexpected challenges. But AZO was able to come to their rescue. In this article, we'll unravel how AZO addressed the unique issues of changing ingredients faced by the "Dry Mix Innovators."
The Company and Its Industry
Our story revolves around a dynamic dry powder mix manufacturer, the "Dry Mix Innovators." They are renowned for producing dry mixes that are loved by consumers across North America. In a bid to enhance their product offerings, they decided to transition from granular sugar to maltodextrin in their mixes. However, this seemingly straightforward switch led to unforeseen complications.
The Challenge: The Maltodextrin Dilemma
The challenge at hand was the unintended consequences of switching to maltodextrin. Both granular sugar and maltodextrin were supplied in bulk bags and entered production through a bulk bag unloading system. This system had been designed to handle granular sugar, but maltodextrin has completely different flow characteristics. Maltodextrin became highly aerated during unloading, which caused it to flood the surge hopper and clog all the filters between the bulk bag and pneumatic pick pan. To compound matters, it also clogged the filter fan which had to be turned off. This created a dust problem which posed an explosion hazard due to the amount of fugitive dust and the explosive nature of maltodextrin.
The Process Evaluation
Upon recognizing this dusting issue, AZO was called in for discussions with the "Dry Mix Innovators." AZO reviewed the operational steps taken, including the fan shutdown, and tested the flow characteristics of maltodextrin to understand the root cause of the problem.
Material Assessment Studies
Product testing is the best way to pinpoint the problem. The maltodextrin tests revealed that it exhibited highly floodable behavior when dispensed from a bulk bag through the unloader. For powders, floodable behavior can be characterized as unstable liquid-like flow. It is caused by the combination of air and the free fall of the powder out of the big bag. This type of flow is both uncontrollable and undesirable.
Engineering Considerations and Innovative Solutions
With a better understanding of the maltodextrin's characteristics and its challenges, AZO undertook a comprehensive engineering evaluation. Flow rates, surge hopper volumes, filter placements, and air-to-cloth ratios were meticulously reviewed. It was determined the maltodextrin discharge rate needed to be slowed down and that the filter should be positioned higher above the surge hopper. To achieve this, an impeller valve was recommended to regulate the flow of product into the surge hopper. Furthermore, a pressure differential indicator was proposed for the surge hopper filter to monitor its performance. "Dry Mix Innovators” loved the solution and gave AZO the order to solve their problem.
AZO's Role in Installation Supervision
Throughout the installation phase, AZO provided invaluable support by offering engineering support and on-site installation supervision. Their expertise ensured that the solution was seamlessly integrated into the "Dry Mix Innovators'" production process.
The Transformation
The result of AZO's improvements were intervention was profound. The system was successfully started up implemented, and for the past few years, has operated smoothly and reliably. Downtime has been minimized, and the fugitive dust (and related explosion hazards) have been effectively mitigated. The success of this endeavor has given the "Dry Mix Innovators" the confidence to consider AZO for future projects.
In conclusion, this collaboration between AZO and "Dry Mix Innovators'" showcases the power of innovation and problem-solving. By addressing the unique challenges associated with maltodextrin, AZO has set new standards for quality and safety. "Dry Mix Innovators” success story with AZO stands as a testament to the transformative impact that can be achieved when two industry leaders collaborate to overcome complex manufacturing challenges.