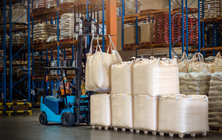
As noted in Efficiency Series Part I: Weighing and Mixing Efficiency, when it comes to bulk powder handling systems, choosing the correct design can be difficult. External limitations, budgets and future expansion plans all factor into system design, and all aspects are business-specific. These systems are not a one-size-fits-all situation. This is why every AZO system is one-of-a-kind, with designs made to fit and adapt to the distinct needs of each client.
Within system design, efficiency remains top-of-mind for AZO engineers. Efficient bulk handling systems are designed to generate the most product in the least amount of time, all while maintaining the highest-possible quality. As mentioned previously, weighing and mixing, and the correct equipment, processes and design is necessary for efficiency. However, there is a second element to efficient systems: discharging efficiency, otherwise known as feeding efficiency.
The first steps of bulk handling address weighing and mixing, while the second phase is concerned with discharge. Once a system weighs and mixes ingredients together, that mixture needs to be discharged by the most efficient means possible.
So what does discharging efficiency look like? “Essentially, to make sure that a system is discharging [also known as feeding or dosing] most efficiently, the discharge needs to be coming out in a consistent, uniform way,” Mike Miller, Vital Sales Manager and Engineer at AZO, explained. “For example, we want to ensure that all of the material coming out of the feeder at any interval is the same quantity, and that we’re not flooding the feeder with the product.”
Much like baking at home, the measurements within bulk handling systems must be very specific. “Because if we’re inaccurate, it makes it hard to know that when we cut off the system, we have captured the right amount of product,” said Miller.
AZO engineers follow three steps to ensure consistent feed, referred to as Fast Feed, Fine Feed, and Pre-Act. Fast Feed is the first component. “This is when we run the feeder as fast as possible,” Miller said. “Once we determine the correct speed, we run it at that speed for as long as we can, and it gets us a basic overall throughput.”
Miller also notes that there is a balancing act between efficiency and speed – “It’s possible to run the device faster than what is ideal, which will decrease the fill efficiency – if we run it too fast, not enough material will fill up the tube that the screw feeder is going through,” he added.
Next, engineers execute the Fine Feed. “Since we know the target weight, we run at a fast feed rate, as fast as we can, without decreasing fill efficiency, then we slow it to a fine feed rate. This allows for better accuracy when it matters most.”
And finally comes the Pre-Act, which deals with the amount of material already in the conveying system. “We know how much material that might be, based on experience and initial system setup,” said Miller. In a small system, for example, that may be one to two pounds, and within a large system that might be twenty to a couple hundred pounds. “Once we reach that weight, we’ll cut off the feeder. Whatever is left in the system is a known quantity, and is how we hit the target weight every time – because we know the amount.”
Consistency, executed by the Fast Feed, Fine Feed and Pre-Act, is essential to efficiency within a discharging system, and our process is regimented and thorough.
And while AZO engineers are always looking to develop the most efficient system possible, our design is always contingent on the specific needs of our clients. “Our typical approach is to meet a customer where they are, help fill in the gaps, help them understand what they're doing and how it relates to bulk powder handling equipment, and to make process improvements so that if their goal is to grow, they have the means to do so,” said Miller. “We can provide the solutions that can accomplish those goals, and they can lean on us as a trusted resource and as a trusted advisor.”