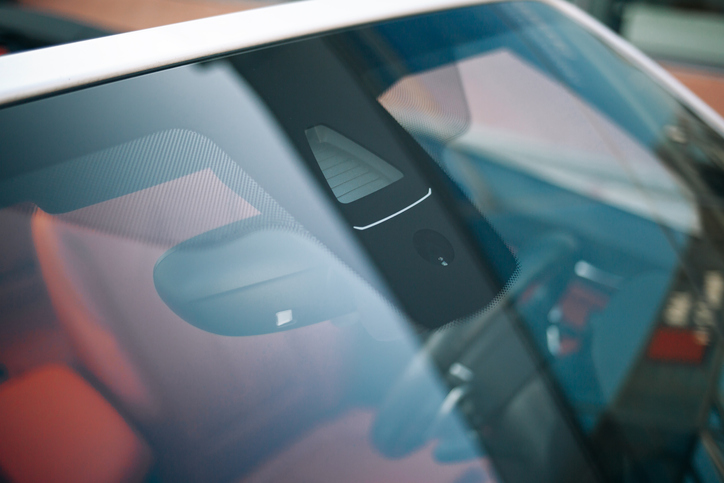
In the realm of safety glass manufacturing, precision is not just a goal; it's an absolute necessity. An AZO customer, Glass Film Specialists," (GFS) produces high quality plastic film which is used to manufacture safety glass for a variety of German automobile manufacturers. The challenge? Ensuring the highest quality film, both strong and completely clear, even when receiving plastic pellets from different batches supplied by their vendor. This is where AZO stepped in to solve the mixing problem in their production process. In this article, we'll explore the fascinating journey of how AZO addressed the unique needs of GFS.
Safety glass is a special type of glass that is specifically designed to be less likely to break and less prone to inflicting injury when it does break. All glass installed in automobiles is safety glass as it is subject to shock or impact during accidents. Safety glass is made by laminating a thin sheet of transparent plastic between two sheets of clear glass. The plastic film needs to be structurally uniform, blemish free and consistent from batch to batch. An AZO material handling system helped to ensure these goals were met.
The Company and Its Industry
Our story revolves around an industry leader, GFS, that specializes in producing high quality plastic film used to manufacture safety glass. Their mission is to create the highest quality film possible, and they understand that consistency in their raw material supply is key to achieving this goal. AZO’s challenge was to ensure a consistent raw material supply that avoided abrupt transitions between batches.
The Challenge: Achieving Material Consistency
While GFS could store more than one truckload of raw material in a silo, they were concerned that slight variations in the raw material batches could cause quality problems. The solution was an innovative silo design which could blend the different batches together within the storage silo. This blending would help to mitigate any potential variations in the raw materials from different batches.
The Process Evaluation
In collaboration with AZO, GFS decided blending silos would address their mixing challenge. No test of the design could be conducted due to the scale of the project, so the design had to be right. The search for an appropriate silo vendor, either in the US or abroad, began. Complicating the challenge was finding a supplier capable of producing a silo of the required size.
Material Assessment Studies and the Quest for the Perfect Silo
Discussions with potential silo builders started with normal designs which could be modified to include a passive mixing tool. The search ultimately led to a specialized German silo manufacturer, with a design that was perfectly suited to the needs of GFS. The silo was produced and shipped to GFS’s production plant in the Carolinas.
Engineering Considerations and the No-Moving-Parts Requirement
The finished silo includes an innovative design – the mixing that is done with a passive mixing tool. The mixing is done inside the silo with no moving parts. Normal mixing technology, which utilizes a rotating mixing screw or auger, would have been a maintenance headache, as the silo would have to be emptied any time access to the machine was required. The passive AZO solution includes a set of mixing vanes, located inside the silo. Mixing is accomplished as the mass flow of the product moves downward inside the silo and through the mixing vanes. This solution is a truly low operating cost, maintenance free, solution!
AZO as the Installation Supervisor
Once the silo and the rest of the equipment arrived on site, AZO played another vital role in the project by providing installation supervision. This supervision ensured that the complete solution was implemented efficiently, and that start up production met the customer's exacting technical requirements.
The Transformative Results
Following the successful implementation of AZO's solution, GFS has enjoyed five years of consistent, high-quality film production. The silo's blending capabilities have ensured that any variations in raw material batches are thoroughly mixed, significantly reducing the risk of inconsistent film quality from the extruder. This achievement has significantly enhanced their manufacturing efficiency and output while maintaining the integrity of their final product.
In conclusion, the collaboration between AZO and GFS exemplifies the power of innovation and problem-solving. By addressing the unique challenge of material consistency in their silo system, GFS can reliably meet the high quality standards that are required of their thin film by the safety glass industry. The GFS success story provided by AZO stands as a testament to the remarkable results that can be achieved when industry leaders work together to solve unique material handling challenges.