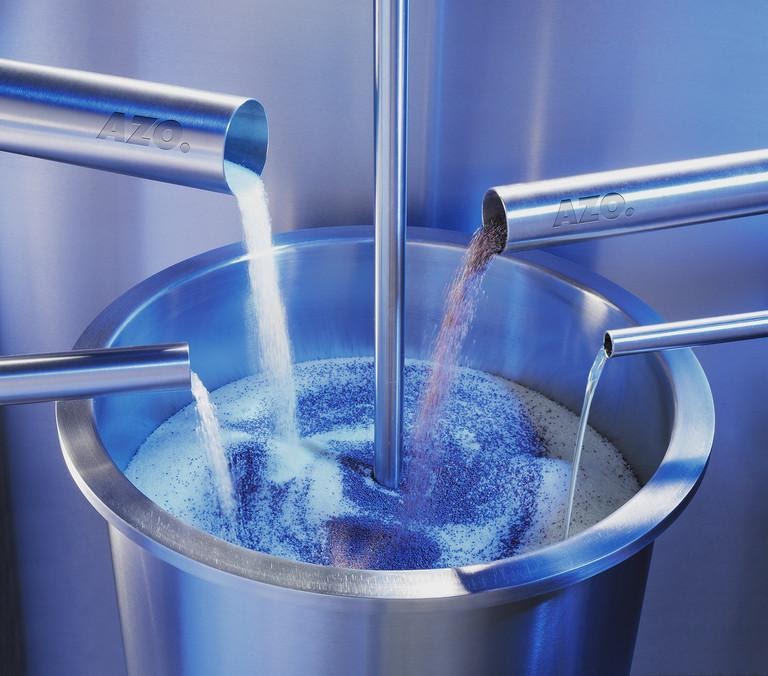
Whether building a batch above a mixer using a scale receiver and gain-in-weight feeder or making a sterile solution in a large liquid tank with a series of loss-in-weight feeders, there are many methods of dosing utilized in the pharmaceutical industry.
An AZODOS feeder built for handling precise amounts of ingredients for processes with a specific design or formula
Many Pharmaceutical companies exclusively handle their batch ingredients manually. This offers plenty of control, but for a growing company, it simply isn’t scalable to continue business this way. Not to mention, there are many possible inaccuracy concerns related to manual dosing. Time and time again we have mentioned the benefits of ditching the “bucket and scoop brigade” for a more efficient handling system, but what about the unexpected twists and turns companies might encounter when they do decide it’s time to scale up?
In the following blog, we’ll explain a few of the critical points of focus that a pharmaceutical manufacturer should always keep in mind when taking the steps to automate systems and scale up to larger automated batches:
Concerns regarding contamination and spacing often surface
Contamination is a concern that keeps coming up in various industries and with good reason. When processing dissimilar products in the pharmaceutical industry, making sure one batch will not contaminate the next is of the utmost importance. Cleaning then becomes absolutely critical. At AZO, we put a lot of energy into separating dry production processes from wet cleaning processes.
Hours can be spent discussing how to mitigate issues related to contamination and also how to solve these problems in a cost-efficient manner. Financial concerns of a new project are usually well known, but often there are also concerns regarding space. Simply put, a new system has to physically fit in the plant space available. Occasionally this consideration is overlooked on the front end, and later the project team is left scrambling when the proposed system won’t fit into the available space.
Flexibility in a system leads to noticeably lower costs
An effective pharmaceutical company is likely one that can be relatively flexible in their processes. Combinations of ingredients can change from day-to-day depending on the product, and there are unique systems that can switch out ingredients with minimal cleaning to accomplish this more efficiently.
Incorporating flexible systems becomes key when looking to save time and cut overall production costs. Specifically, AZO offers an innovation called the DOSITAINER® for those seeking truly flexible production keeping in mind “what we do today might change tomorrow.”
We’ve explained the benefits of the DOSITAINER® before, but essentially a dosing screw feeder is installed in each bin. This addition makes it possible to achieve faster ingredient changeovers since operators don’t have to deal with residual product left in a fixed or stationary screw feeder. In the DOSITAINER®, only the drop-tube will need to be cleaned before another IBC (with a new ingredient) is dropped into place in the production line — enabling true “plug-and-play” functionality. Faster product changeover reduces downtime and lowers production costs.
Accuracy is greatly increased by automated dosing
The accuracy of scaling systems directly influences the consistency of pharmaceutical products. Leaving batches open to the possibility (and inevitability) of spills from buckets and scoops simply cannot produce as consistent a product as one produced in a closed batch system. An additional benefit is available if barcoding is implemented. This allows tracking and tracing of each batch produced. Knowing exactly what is produced and how much you have is critical in situations like product recalls.
These functions are repeatable, and consumers can count on a reliable product. We know it can be difficult to achieve lower costs and still achieve accuracy in your dosing process. Still, ensuring dosing accuracy is something AZO has done for decades.
AZO strives to take as much of the accuracy-related tasks out of operators’ hands to ensure the quality and consistency of your products (day in and day out). If you’d like to hear more about our COMPONENTER® systems, feel free to download the free e-Guide available on our site. You can also contact our team of sales engineers for any other queries on automating ingredients or conveying materials. AZO has decades of experience in the ingredient automation world and tons of topics we’ve covered on our blog.