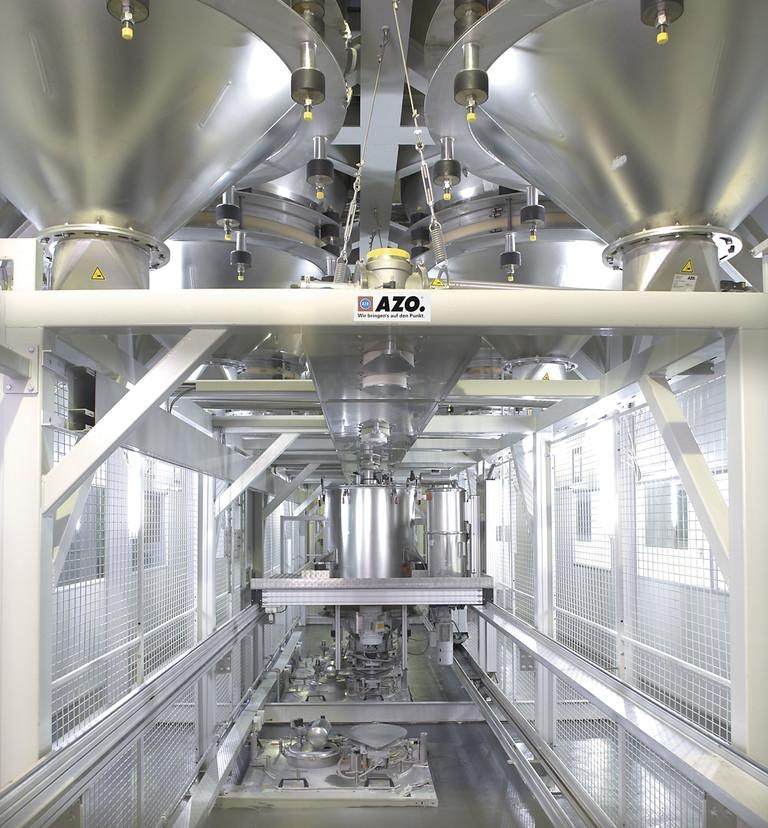
Precisely getting each micro ingredient in every formula every time: This is what introducing automated ingredient systems into a process can achieve. Buckets and scoops will only get you so far when recording and tracking data for minor and micro ingredients.
We know it can be difficult to justify an entirely new system unless it can be assured that the system will truly meet the ROI hurdle. Still, an automated batching system can reduce or even eliminate the tedious manual weighing that often leads to various inaccuracies and product inconsistencies. Like other machines in the world of ingredient automation, these systems can also help keep your employees safe.
You want your mixes and ingredients consistent for every batch no matter where your products end up. With ingredients that vary over a wide range of weights and flow characteristics, how do you track them accurately in your process to achieve this? The AZO-specific solution for this challenge is our COMPONENTER®, and in this post, we’ll share how the savings and safety benefits of installing a COMPONENTER® make for a faster and more accurate operation.
Accuracy increases when automating minor and micro ingredients
In an open batching system, you have a chance for error, spillage or foreign materials to enter into the process. The quality and consistency of a product all come down to the accuracy of scaling systems on a repeatable basis (day in and day out). With the combination of a barcode scanner and an automated batching system (especially a COMPONENTER®), you can accurately track and trace ingredients to keep up with them.
Think for a moment — each and every time a worker scoops material into a bucket on a platform scale, there exists the likely chance that some amount of product will be spilled. No matter the degree of focus that a pair of steadfast hands may have, we know that spills happen when manually weighing materials. Unfortunately, mistakes such as these could absolutely lead to consumers choosing other products from your competitors. True product quality, again, begins with accuracy and consistency in batch processes.
Safety is more assured by automating processes
Not only can a machine such as a COMPONENTER® improve the consistency of the products made with micro and minor ingredients, but workers that once operated the bucket and scoop brigade can now potentially focus on safer and more meaningful endeavors. Many times these operators that once were required to reach from a platform to dump hundred-pound bags (and inhale dust throughout the day as they do so) can instead be in the control room keeping track of production instead of performing monotonous and dangerous tasks.
Installing a COMPONENTER® can and will save on labor costs in the long run, but the safety benefit of automating your minor and micro ingredients shouldn’t be understated. Workers’ compensation insurance claims introduce huge liabilities. Direct costs that follow injuries can include compliance penalties. These claims cost, on average, $134,940 (according to OSHA and the U.S. Department of Labor in January 2020). It might be time to introduce an automated system to take care of your minor and micro additives, especially in areas that have experienced multiple workplace injuries.
At AZO we strive to take as much of the exposure-related tasks out of operators’ hands to ensure the quality and consistency of your products (day in and day out) wherever they may end up. For more insights on the benefits of ingredient automation and the time-tested robust equipment that AZO provides, don’t hesitate to download our free COMPONENTER® e-Guide or contact our dedicated team of sales associates.