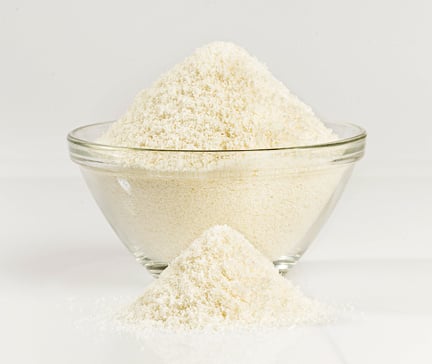
Bulk materials and their (flow) properties are diverse and careful consideration must be given to handling them. Rather, they challenge every plant manufacturer and engineer working in this field anew every day.
This is exactly the kind of challenge we love at AZO and have been able to tailor and adapt our products and processes to our customers' raw materials for over 75 years.
In this session, we deal with the challenges associated with discharging and processing of pulp-based fibers and chopped goods, which play an important role in recycling processing, among other things.
Together with our customers and manufacturers of such materials, AZO has further developed and improved its big bag unloading station in a way that highly bridging raw materials come out of big bags efficiently and safely without having to intervene manually.
For example, if you look at a cellulose powder, at first glance this looks very similar to cotton wool or cotton. And it is, as it is a natural fiber-based product that is used in a variety of industries, from construction materials or automotive parts to the food and pet food industry, which are particularly important for AZO, as well as in the plastics industry.
Due to the lightweight nature of these products and their ability to be easily compacted, they serve as initial indicators of potentially challenging flow or storage conditions. This, among other factors, complicates traditional big bag discharge, where the material is typically moved to flow, by using mechanical shakers or massagers.
But even as bagged goods in smaller volumes, such a fibrous powder, which can also be very fine, is not easier to handle. As material in the bags often compacts into firm bales and in addition, the bags are very large due to the low bulk density – which makes ergonomic processing almost impossible.
As part of our development work, AZO was able to gradually develop and test a design that not only enables a more than acceptable discharge time, but also enables the almost even more important further processing in the long process chain directly. At AZO, the focus shifts from the original task to a holistic solution, which may make the framework conditions more difficult.
For example, emptying the big bag by opening the entire bottom, and discharging a solid mass of material is not an ideal solution, because we would have solved one task, but created an additional task for our customers: solving the puzzle of where to put the solid mass? Which process technology can handle a 1m x 1m solid mass?
The overall system must address all challenges, including safe application for the operator, low-dust processing, as well as downstream process chain concerns, where transport, storage or high-precision dosing may be necessary.
This leaves us with the option to use either a bag dump station that can receive and dissolve compacted lumps of fibers and process them accordingly, or to a big bag unloading system with a secure support platform and a low-dust docking that feeds into the downstream process.
At AZO, we have answers and products that meet all the requirements for such difficult-to-process raw materials and meet our customers' wishes for safety and ergonomics without racking.
By utilizing FEM analyses and 3D modelling, a new discharge platform for big bags was designed, which creates a special vibration behavior adapted to fibrous products, so that they find their way to the outlet in a deliberate manner. What is not possible at all on a standard system or only with extreme time and manual effort, can be done in approximately 10 minutes on the modified system with the same raw materials, in big bags of up to 2000 L volume.
Interim storage in day bins is just as possible, as safe pneumatic transport to the final receiving destination, where it is then precisely weighed and dosed into a mixer, or fed into any other process.
Energy-efficient and safe discharge aids on a mechanical or pneumatic basis enable the best discharge results, so that bridging, caking or funnel flow has no chance.
This gives customers flexibility in how to receive raw materials with solutions on how to handle these materials in subsequent steps in the process – we at AZO have the right overall solution for everything.
… and one last note at the end: If you compare the two packaging formats (bags vs. big bags) with each other, it is easy to see that the processing of 10kg – 15kg bags (more is not possible with such low density materials) require considerable additional effort.
On the one hand, operators are stuck performing low value tasks when emptying bags, with small emptying capacity and increased waste expenditure.
On the other hand, the exposure to ergonomically demanding and physically intensive work, as well as the permanent exposure to dust, or to wearing appropriate protective equipment, are much higher compared to processing big bags.
At AZO, we can handle all formats and are happy to offer you a tailored solution for your challenge – even in an explosive atmosphere!
Design Highlights:
- Ergonomic and safe design, easy to operate
- Integrated dust control, without any material losses
- FEM analysis and 3D-based design guarantee the durability and longevity of the equipment
- Excellent discharge time for poorly flowing materials
- Flexible integration into existing or new production process