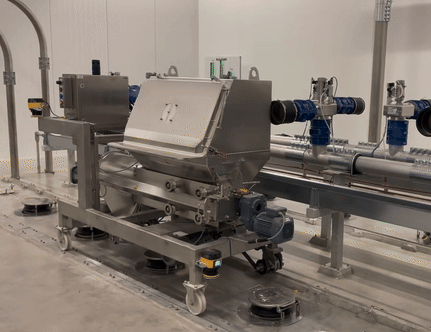
In today's rapidly evolving technological landscape, innovation is key to staying competitive. One such innovation making waves in the manufacturing sector is the mobile screener application, specifically designed to enhance efficiency in food processing environments. In this post, we’ll dive into the development and deployment of a mobile screener application for a food manufacturing project that AZO is managing. This innovation is designed to handle multiple ingredients efficiently, with minimal operator intervention and significant cost savings.
The Genesis of the Mobile Screener Application
The mobile screener application was conceived to address specific challenges in a food manufacturing project handled by the AZO team. The project's primary goal was to create a solution that could effectively screen a wide variety of ingredients with minimal cross-contamination and reduced operator handling. Initially, the team considered using dedicated bag dumps with screeners for each ingredient; however, this approach was deemed too costly. Another consideration was to use a common bag dump station with a screener, which would convey the ingredients to dedicated storage receivers but cross-contamination issues made this solution not viable.
Instead, the team decided to leverage a mobile cyclone screening technology, an idea inspired by an innovation document from our AZO GmbH colleagues. This technology, although not new, was adapted to fit the project's needs by combining past experience with new, automated positioning systems. The result was a mobile screener that could move autonomously along a track, reducing alignment issues and operator intervention.
Overcoming Challenges in Practical Application
Despite the innovative design, the implementation of the mobile screener was not without its challenges. One significant issue was the residual product left in the hopper part of the screener. Even though the mobilization aspect worked well, aligning the docking stations with the hoppers posed a challenge due to floor misalignments and structural variations in the manufacturing environment.
The design was initially tested in a warehouse setting where the floors were level, but real-world manufacturing environments presented different challenges. The team had to make several modifications to accommodate these practical realities, such as adjusting the docking height of the screener and installing air sweeps inside the screening chamber to clear residual powders more effectively. These adjustments were necessary to ensure the screener operated efficiently across all stations without significant operator interaction.
Key Features and Benefits of the Mobile Screener
- Cost Efficiency: By utilizing a single screener to manage multiple ingredients, the mobile screener significantly reduces the cost associated with deploying multiple stationary screeners.
- Minimized Operator Intervention: The automated positioning system reduces the need for manual alignment, allowing operators to focus on other critical tasks.
- Reduced Cross-Contamination: The mobile screener's design minimizes cross-contamination risks by effectively separating different ingredients during the screening process.
Customer Feedback and Future Enhancements
Customer feedback has been largely positive, with many appreciating the reduced operational costs and increased efficiency. However, some concerns remain about the residual powders left in the screener after each use, which could lead to cross-contamination if not properly cleaned. The team is actively working on solutions to mitigate these issues, such as enhancing the cleaning protocols and possibly integrating more advanced air sweep systems.
Future enhancements may include further automation to handle even more complex ingredient combinations and reduce the cleaning time between batches. Additionally, the system was designed with expansion for more ingredients in mind and the customer has indicated they plan to add additional stations to the current system.
The mobile screener application is a prime example of how innovative thinking and technological adaptation can solve complex manufacturing problems. While challenges remain, the progress made thus far demonstrates a significant leap forward in efficient, cost-effective food manufacturing. By continuing to refine this technology, the team aims to set a new standard in the industry, enhancing productivity and ensuring high-quality outcomes in food manufacturing.