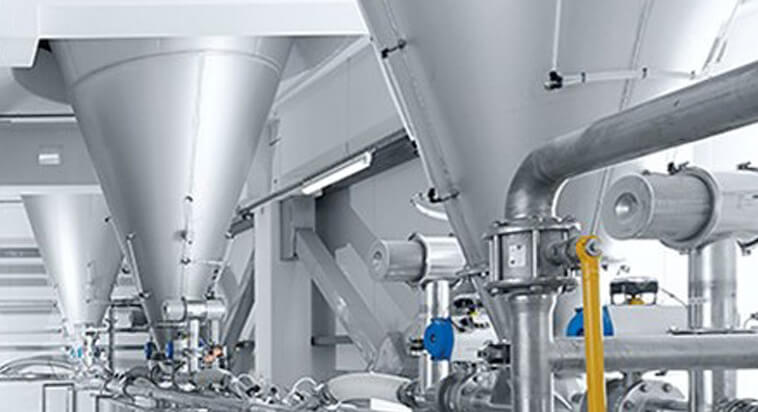
Optimizing older systems is crucial to maintaining efficiency and extending the life of valuable equipment in today’s dynamic industrial environment. Here at AZO, we recently conducted a comprehensive optimization project on a system installed in 1999, proving that even decades-old technology can run at optimal levels with the right service and maintenance. In this blog, we’ll talk about the process and the key lessons learned throughout.Background: Why Optimize a 25-Year-Old System?
Many companies rely on older systems that continue to meet their production needs. However, as these systems age, inefficiencies can creep in, leading to reduced output and increased costs. In this case, the customer wanted to ensure their six existing mix lines were running at full capacity before investing in a new mixer. This approach highlights a deepening trend in industry to maximize the utility of existing systems before making significant capital expenditures.
Initial Assessment: Starting with the Filters
One of the first areas AZO’s service team, led by Mike Nichols, focused on was the pneumatic conveying system’s filters. Filters are a critical component in any such system, and they need regular servicing with attention to detail.
Key findings included:
- The filters were being over-cleaned with 110 psi of compressed air, which is significantly higher than the recommended 60-80 psi.
- Over-cleaning the filters caused leaks, leading to product buildup in the clean air side of the filters.
- This issue not only slowed down the conveying process but also led to inefficiencies and damage in other parts of the system, such as the blowers.
Resetting the filters to the correct psi and cleaning schedule was the first step toward optimizing the system's performance and achieving significant savings in compressed air pressure.
Fixing Fluidizers and Discharge Valves
Another critical issue were the fluidization units, which help discharge products from the scales. These were set at too high a pressure and frequency, leading to a significant delay in the discharge process—up to five minutes per batch, instead of the usual two or three minutes.
The team adjusted the settings and repaired faulty units, significantly reducing batch times and improving overall system throughput.
Piping and Integrity Checks
To ensure the system was airtight, a vacuum integrity check was performed. This involved covering the inlet filter on each line and testing the vacuum pressure to detect any leaks.
Key actions included:
- Checking the blowers, belts, and relief valves.
- Testing the vacuum integrity by pulling the system down to 7-12 inHg and monitoring for leaks.
- Walking the entire line to identify any faulty seals or diverter valves.
This step was crucial to ensuring that the system was operating efficiently.
Optimizing the Silos
The plant has both outdoor and indoor silos, which require special attention due to their exposure to different environmental conditions.
For the outdoor silos:
- The team checked for UV damage on plastic hoses, seals and reset compressed air.
- Pressure Vacuum Relief (PVR) valves were checked for leaks.
For the indoor silos:
- Similar to the outdoor units, the filters and PVR valves were checked.
- Vibration bottoms and isolation rods were inspected to ensure they were functioning correctly.
These checks ensured the silos could continue to store and discharge product without causing delays or damage to the system.
Results: A More Efficient System
After two weeks of intensive maintenance and optimization, the plant was running at 80% capacity; a significant improvement for a system that had been in place for 25 years. While not yet at full capacity, the results were promising enough that the team scheduled a follow-up visit to further optimize the system and get it back up to 100% capacity.
This optimization project demonstrates the importance of regular maintenance and correct settings. Overusing compressed air and not repairing small issues like leaks or faulty valves can cause significant inefficiencies over time.
Lessons for Optimizing Older Systems
The successful optimization of this 25-year-old system provides valuable lessons for anyone operating aging industrial equipment:
- Regular Maintenance is Essential: Even well-built systems require regular checks and adjustments to stay efficient.
- Don’t Overlook the Small Stuff: Simple components like filters, valves, and pressure settings can have a huge impact on overall performance.
- Measure and Optimize: Routinely conduct integrity checks and measure system performance to identify areas for improvement.
By following these principles, companies can extend the life of their systems and avoid costly upgrades or replacements. As industries continue to look for ways to save on capital expenses, optimizing existing systems is a smart and cost-effective approach.
Contact us to learn more about how AZO can optimize and improve your ingredient automation systems.