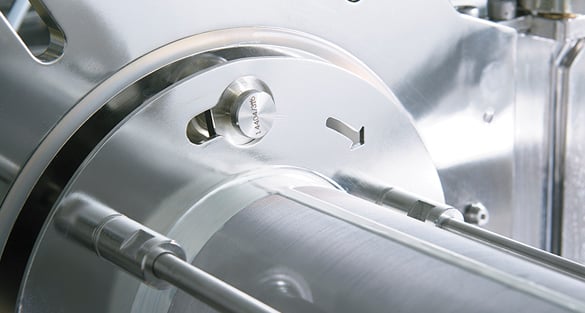
Screening powder paint involves feeding the material through an AZO centrifugal screener to ensure optimal performance and coating quality. This process addresses common challenges such as clumps, contaminants, or oversized particles that can form during manufacturing, transportation, or storage.
Benefits of Screening Powder Paint
- Improved Coating Quality
- Smooth Finish: Ensures only fine, uniform particles are used, resulting in smoother and more consistent coatings.
- Defect Reduction: Removes contaminants and oversized particles that cause surface imperfections like bumps, pinholes, or uneven coverage.
- Enhanced Application Efficiency
- Consistent Flow: Uniform particle sizes reduce clogging and enhance the flow through application equipment.
- Better Adhesion: Optimized particle distribution promotes better adherence during application.
- Reduced Waste
- Recyclability: Screened powder can be reused effectively, reducing waste and extending usability.
- Cost Savings: Minimizes rework and the need for additional layers by eliminating defective materials upfront.
- Protection of Equipment
- Clog Prevention: Screening eliminates clumps and contaminants that may block spray guns or feed lines.
- Reduced Wear: Minimizes wear and tear on equipment, lowering maintenance costs.
- Consistency in Appearance
- Uniform Look: Prevents impurities from altering the final color and texture, ensuring consistent finishes across all parts.
- High Aesthetics: Critical for decorative or highly visible surfaces.
- Simplified Quality Control
- Easier Diagnosis: Ensures consistency in materials, aiding in defect source identification.
- Compliance: Helps meet industry and customer specifications.
Screening Best Practices
- Mesh Selection:
- New or virgin powder should be screened into a clean, dry hopper using an appropriate mesh size. Manufacturers typically use an 80-mesh screen (177 microns); however, for high-quality finishes, a 100-mesh screen (149 microns) can be used. This finer mesh removes heavier particles, crucial for achieving blemish-free surfaces.
- Addressing Common Problems:
- Powders often compress during storage or transport, leading to clumps. Screening prevents these from clogging feed lines and causing puffing or surging.
- Proper equipment settings and maintenance are essential to achieve maximum transfer efficiency and finish quality.
Importance of Centrifugal Screener Maintenance
Daily maintenance ensures the equipment operates efficiently and avoids powder paint issues:
- Screen Installation: Screens must be straight, with mesh openings uniform and square.
- Seal Integrity: Rear screen frame seals should be soft and correctly installed to prevent powder leakage.
- Air Purge Systems: Avoid metal-to-metal contact to prevent heat buildup and melting.
- Daily Checks: Inspect screen condition, maintain seal pressure (7-10 psi at 3.5 CFM), and monitor air purge seal integrity.
Related Blog Posts
Ice cream remains one of the most popular desserts worldwide — available in countless varieties and flavors. Despite recipe differences,
Manufacturing is at a turning point. For operations that depend on high-throughput, preciseingredient handling, the real threat isn’t just