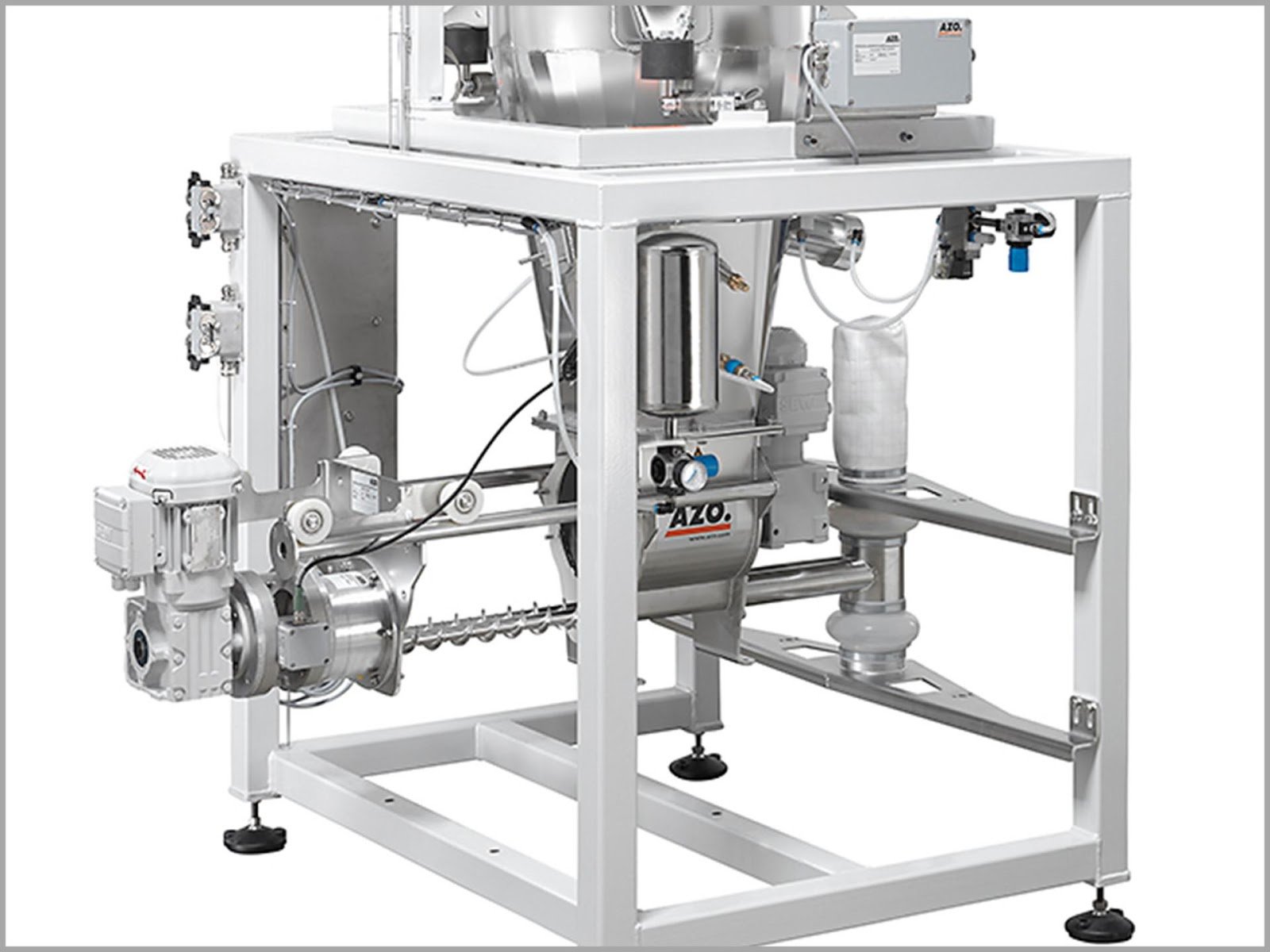
There are two basic types of feeders in the world of ingredient automation: gravimetric and volumetric. Volumetric feeders control and measure the specific volume in the speed of material entering a system. Gravimetric feeders, on the other hand, control and measure based on weight in the speed of materials leaving a feeder.
The feed rate of a volumetric feeder is controlled by the auger speed, which is based on testing and tuning. A key difference with volumetric feeders is that they don’t automatically compensate for changes in a material’s density. Essentially, there’s no direct measurement of product throughput with a volumetric feeder.
As we’ve covered how continuous operations benefit from a loss-in-weight feeder (a type of feeder categorized under gravimetric feeders), in this post, we’ll expand on the types of applications that call for volumetric feeders and explain how they operate in different systems.
Batch systems can operate through gain-in-weight and negative scaling
While continuous feeding moves product to machines consistently and constantly with a gravimetric feeder, batch systems dose material by weighing discrete amounts of each product as required for each batch. In a gain-in-weight system (see diagram below), the volumetric feeder dispenses product into a hopper that is on load cells (indicated by orange triangles). As you feed out of the bin above into the lower hopper, you see a weight gain in the lower hopper.
The AZODOS DV model is a volumetric feeder that can operate through gain-in-weight scaling. The DV model’s load cells (orange triangles) are located under the hopper. Any AZODOS model will have a much greater degree of accuracy and can assist poor-flowing products more effectively than standard screw feeders or rotary valves.
In a negative scaling system, a gravimetric feeder is utilized during some batch operations. As product is taken away from the feeder, that limited amount of product is measured. For instance, if a batch process calls for 50 pounds of product, 50 pounds (no more or less) is subtracted from the total weight of the hopper and feeder.
The AZODOS DW model’s load cells (orange triangles) are located on the feeder. The DW can operate through negative scaling for batch operations. It can also be utilized in continuous operation (albeit without the ability to make adjustments to the auger speed while feeding like a loss-in-weight feeder can).
Typically, volumetric feeders are less expensive than gravimetric feeders. Still, there’s one specific component that can make opting for a gravimetric feeder necessary.
Accuracy is critical in gravimetric systems
When you don’t necessarily need to know exactly how much material is being put into a process, a volumetric feeder becomes applicable. On the other hand, gravimetric feeders are instrumental in operations that require a great deal of accuracy. When small variations in what you’re being fed will make a major difference to the end product, it is best to implement a gravimetric feeder because the amount of material being taken away (at a given speed) is deciphered by the load cells and control system.
A loss-in-weight feeder that has load cells ultimately has a greater degree of control. It can make adjustments to the speed of the auger based on the weight being taken away. Still, when accuracy is not a prioritized concern (and you’re just trying to feed a constant stream of product regardless of bulk densities), a volumetric feeder is perfectly applicable.
When feed-rate requirements are high, capital costs can be expensive
We’ve mentioned before that capital costs for different types of feeders will generally depend on the required feed-rate. When the feed rate requirement is high, the capital cost associated with a gravimetric feeder can become prohibitively expensive. One solution could be a weighbelt feeder in these specific situations.
If you have any questions about the AZODOS feeder models and their compatibility between batch versus continuous feeding, contact a dedicated AZO sales associate. You can also check out our blog for more tips on pneumatic conveying and ingredient automation.