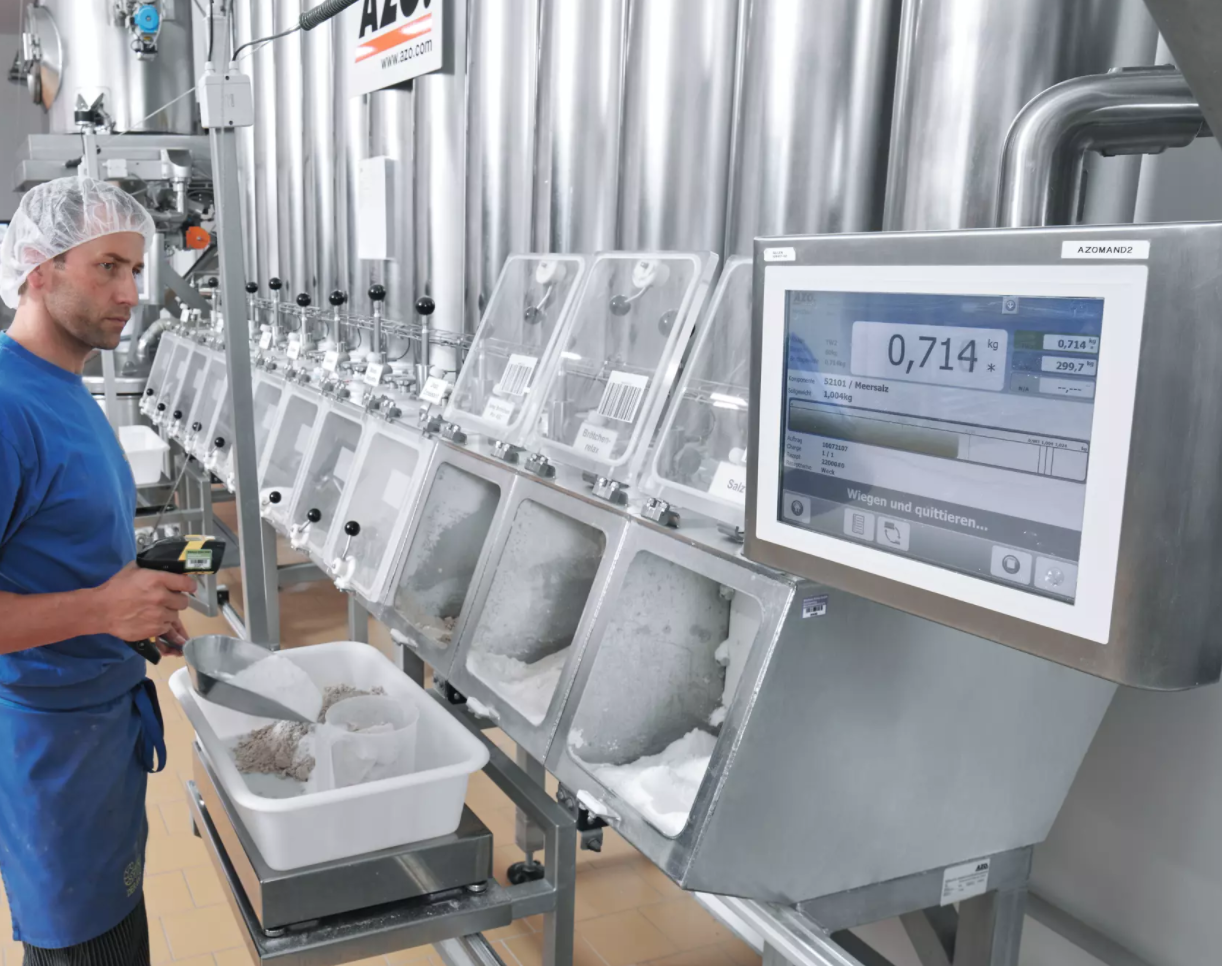
How AZO’s Individualistic Design Approach To Bulk Powder Handling Equipment Achieves Efficiency For Customers
Choosing the correct bulk powder handling system for a business can be an incredibly difficult task, with a number of internal and external limitations, budgets, and future expansion plans complicating the matter. These systems are not a one-size-fits-all situation – Which is why every AZO system is one-of-a-kind, with designs made to fit and adapt to the unique needs of each AZO client.
The AZO design process is a two-pronged approach in which AZO engineers expertly assess two questions: What are the limitations of what can be accomplished? And what is the “Good, Better, and Best” for each situation?
The first prong involves an appraisal of the client’s unique needs and limitations. “We approach every customer inquiry the same way,” explained Mike Miller, Vital Sales Manager and Engineer at AZO. “I learn what the inputs are. What are the materials that we are handling? What are their requirements for their overall process – how many finished goods are they producing? What does the physical space look like? Those systems will look very different and will require different technologies to accomplish the same overall task.”
After the inputs are diagnosed, Miller and other AZO engineers work to create a specially tailored system based on the current and future needs of the client. “We design the concept using basic concepts of material handling technologies and turn it into an AZO system, share that with the customer and receive critical feedback,” said Miller.
The second of the two-pronged approach to system design – the “Good, Better, and Best” approach – is based entirely on efficiency, and what level of efficiency makes the most sense for each client.
Efficient bulk handling systems aim to generate the most product within the least amount of time while maintaining the best quality possible. Most often this means separating out processed tasks in the weighing stage and accomplishing them simultaneously, thus making the overall process more time efficient and producing a higher product yield. There are two major areas in which efficiency is absolutely necessary: weighing and mixing.
Weighing and mixing efficiency are interrelated processes, as all of the individual ingredients must be weighed before being mixed together into the final product, as is with any standard recipe. Both processes become increasingly more efficient if each batch of ingredients is weighed concurrently as opposed to sequentially.
“Sometimes we don’t have enough room for a large scale and have to successively weigh up the amount of material required [on the same piece of equipment],” said Miller. “This will likely take two to three times as long to weigh as it would if we were weighing all the material at once. Or, we would have to convey and weigh at a greater rate to make up the time it takes to do that task.” Essentially, if multiple weighing devices are implemented in a design system, the amount of time required to create a product is vastly reduced.
With weighing and mixing efficiency top of mind, AZO engineers are able to assess the “Good, Better, and Best” for each situation. “A Good situation is using the mixer as the weighing vessel. With this design we may only be able to achieve an output of 3 batches an hour, when we really need 6 batches an hour,” explained Miller. “Better,” he said, “is pre-weighing a whole batch in succession in a hopper scale or a scale receiver, while the mixer is mixing. Instead of possibly 3 batches an hour, we may be able to achieve 5 batches an hour by simultaneously weighing and mixing.”
And finally comes “The Best” situation: “If we add another scale to the system and have separated out the bulk ingredients from the minor ingredients, we can now achieve the needed 6 batches an hour – or even 7 to 8 batches an hour. In this scenario, AZO has provided a system designed for future growth without having to add in a whole new system.”
AZO engineers are particularly drawn to the “Best” design approach because it leaves room for growth. “Say, for example, we have a customer that says they want a system that can do X today, but will do 20 percent more two years from today, or 50 percent more three years from today,” said Miller. “We will design with that future build in mind so that our system can grow with them and they’re not having to redesign and retool their process every couple of years.”
And while AZO engineers are always looking to develop the most efficient system possible, their design is always contingent on the specific needs of their clients. “We’re not a best-fit kind of situation, everything we do is custom-designed. We have standards for individual pieces of equipment, but how those pieces of equipment fit together in a complete process system is unique to each of our customers,” said Miller.
AZO engineers are here to meet a client where they are, and help them understand how that client’s individual business relates to bulk powder handling equipment. “We can provide the solutions that can accomplish those things,” explained Miller. “They don’t have to be experts in powder handling equipment, they can lean on us as a trusted resource and advisor.”