Bulk Ingredient Weighing & Batching
Introduction
Whether used in food, pharmaceuticals, chemicals, or countless other industries, accurate bulk ingredient weighing and batching is a critical component in ensuring product quality, consistency, and safety. Each ingredient's proportion within a mixture, known as batching, contributes to the end product's taste, texture, functionality, and more. Only accurate ingredient weighing can achieve a delicate balance of flavors in food manufacturing or the precise formulation of pharmaceuticals.
Precise bulk ingredient weighing is also critical for resource optimization. In an era where sustainability and cost-efficiency are paramount, attaining the exact amount of each ingredient for every production batch required results in less waste. Accuracy in weighing avoids excess that must be scrapped, translating to reduced costs and environmental impact.
Additionally, regulatory compliance hinges on precise measurements for each production batch. Certain industries must adhere to stringent government standards that demand accuracy in ingredient proportions. Any deviation can lead to compromised product quality and regulatory violations. In this context, bulk ingredient weighing and batching serve as safeguards against deviations, ensuring that every batch, of every product, meets regulatory benchmarks.
Benefits of Bulk Ingredient Weighing and Batching
Consistent Product Quality
Precise bulk ingredient weighing consistently delivers accurate ingredient proportions. From food and beverages to pharmaceuticals, this precision translates into uniform product attributes, ensuring each batch consistently matches the desired specifications. Automated batching takes common human errors out of the process, raising the quality standard compared to manual measurement. Either way, quality variations due to inconsistent ingredient ratios should always be eliminated.
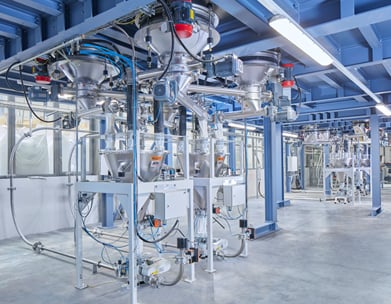
Operational Efficiency
Automated bulk ingredient weighing optimizes efficiency by reducing the likelihood of material waste. It can also speed up the production process. Machines can operate 24 hours a day, 7 days a week without taking breaks. It also allows improved transaction and batch tracking. Production never has to stop due to a lack of ingredients.
Regulatory Standards
Industries operating under stringent regulations benefit immensely from automated bulk ingredient weighing. Regulatory standards demand accuracy in product formulations, with non-compliance leading to severe consequences. Precise weighing and batching systems defend against regulatory violations by ensuring products consistently adhere to prescribed benchmarks.
Waste Reduction
Accurate bulk ingredient weighing also reduces waste. By minimizing ingredient measuring variances, precise weighing contributes to sustainable practices and reduces scrap or rework costs. This also supports responsible manufacturing production and minimizes contributions to the waste disposal stream.
Production Flexibility
Adaptable to diverse production needs, automated bulk ingredient weighing systems accommodate changes in batch sizes and material variations. This flexibility is particularly critical for new product formulations. It can also accommodate fluctuations in material characteristics due to humidity or clumping during storage.
Factors to Consider when Choosing Bulk Ingredient Weighing and Batching Systems
Material Characteristics
Understanding the unique attributes of any bulk ingredient to be weighed is paramount for effective design. Factors such as density, particle size, and flow characteristics directly influence the selection of an appropriate weighing and batching system. Fragile powders, for instance, require gentle weighing, while denser granules may adversely impact a weighment with tight variance targets. Flowability also directly impacts weighing. Materials that are prone to compaction are a challenge to effectively weigh. Excessive flowability has the opposite effect; the design must incorporate checks to limit certain materials’ natural tendency to move too easily.
Throughput Capacity
Determining the required throughput capacity of the bulk ingredient weighing system is fundamental. Whether the production demands are high or low, selecting a weighing system that matches the required speed is crucial for efficient batching. Underestimating throughput capacity can negatively impact batch production timelines and adversely impact mixing utilization.
Measurement Accuracy
The accuracy of the weighing system directly impacts product quality and regulatory compliance. Depending on the industry — such as pharmaceuticals or chemicals — stringent tolerances may be required. On the other hand, it is possible to design an overly accurate weighing system that is needlessly expensive. Designing a system with the appropriate accuracy ensures consistent product attributes and an economic good fit.
Flexibility and Adaptability
Industries are dynamic, so production needs to be flexible. Choosing a bulk ingredient weighing system that can accommodate varying batch sizes and ingredient variations is essential. This flexibility future-proofs operations and enables seamless adaptation when market demands change.
Integration with Existing Processes
Seamless integration of a new automated weighing and batching system into existing production processes is a necessity for a successful investment. Ensuring compatibility with existing equipment, control systems, and data management requires designs that are thorough and well thought out. The optimal design enables fast start-up and debugging to minimize production shutdowns and to ensure accurate and efficient production.
Maintenance and Support
The long-term performance of the chosen weighing system relies on regular maintenance and, when adjustments are needed, available technical support. Opting for a system with user-friendly maintenance features, software that regularly validates weighment accuracies, and reliable support services ensures batches will consistently meet technical specifications. Ultimately, weighing is a mechanical process that requires continuous monitoring. It’s not a matter of if, but rather when, adjustments and maintenance will be required.
Budget and Cost Analysis
Balancing system requirements and capabilities is an important capital cost consideration. Striking the right balance between functionality and accuracy is critical for budget constraints. This is essential when designing a technically appropriate and cost-effective automated bulk ingredient batching system.
Questions About Bulk Ingredient Weighing?
AZO’s Bulk Ingredient Weighing and Batching Systems
Understanding that bulk ingredient weighing and batching can vary widely among different manufacturing operations and industries, AZO offers a range of weighing and batching solutions. AZO’s precision batching systems are tailored specifically to meet different material, accuracy, and operational needs. AZO’s various weighing systems employ different techniques to meet both technical and budget requirements.
Batch Weighing
This method involves weighing several different ingredients simultaneously, as required for batch production. It's a practical approach when multiple ingredients are being loaded into the processing machine at the same to create a unique production batch. AZO’s Batch Weighing equipment streamlines the weighing process and maximizes the batch production line throughput.
Continuous Weighing
This technique is ideal for continuous production applications that demand a constant and uninterrupted flow of materials, such as extruders used in food and plastic manufacturing. AZO’s Continuous Weighing systems provide real-time measurements as materials are in motion, guaranteeing consistent proportions.
Gravimetric Batching
Engineered precision is the hallmark of AZO’s Gravimetric Batching systems, which measure ingredients based on weight to maintain precise ratios as required for recipes. This method is ideal for industries where even slight deviations can impact product quality, such as pharmaceuticals or electronics manufacturing or for high-cost materials.
Dynamic Weighing
Dynamic weighing is the go-to for measuring materials in motion, such as those being dosed into continuous processing equipment like extruders. Dynamic weighing seamlessly integrates into fast-paced continuous production processes. AZO’s equipment is designed to deliver accurate measurements when the continuous production must remain within specification 100% of the time.
Static Weighing
Static weighing is employed when materials are at rest, typically in vessels or hoppers. It's a method commonly used in scenarios where individual materials need to be measured before being blended or combined. AZO’s equipment is engineered to preserve accuracy, minimize discrepancies, and deliver years of reliable service.
Trust AZO When Choosing a Weighing and Batching System
When it comes to selecting a bulk ingredient weighing and batching system, AZO’s solutions deliver both precision and engineering expertise. With experience in a diverse range of industries, AZO delivers tailored solutions that seamlessly integrate into existing processes. With a commitment to pushing technological boundaries, AZO’s engineers ensure that systems that exceed expectations, while comprehensive support services guarantee a reliable, long-term partnership.
By investing in a robust bulk ingredient weighing system from AZO, manufacturers can maintain their commitment to delivering high-quality products while optimizing accuracy and production speed.
Resources About Bulk Ingredient Weighing
Solutions
AZO Mixomat
An economical solution for transporting, dosing, weighing, and mixing that is well-suited for discontinuous, gravimetric loading.