Due to its fine particle size and light weight, handling ingredients like fumed silica can be exceptionally difficult. Prone to sticking, clumping, or bridging, it can easily clog filters, bins, or conveyor lines. Fumed silica’s unique properties must be considered when selecting methods of material storage, conditioning, conveying, emptying, and dispensing.
Fumed Silica Handling Solutions
Used as a thickener in a wide variety of industrial products, fumed silica’s unique characteristics require experienced design and engineering to optimize its bulk material handling.
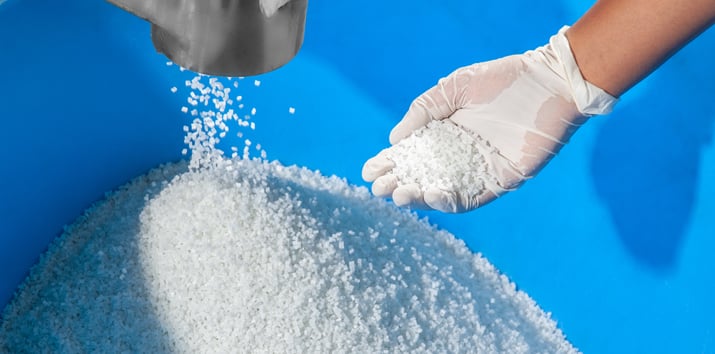
Fumed Silica Handling: Overview
Composed of very fine, non-porous particles of silicon dioxide (SiO2), fumed silica powder has a high surface area and light density. Due to its extremely high surface area, it is an effective thickening and reinforcing agent in many products. Whether it’s used in personal products, poly and plastics processing, or chemicals, fumed silica’s unique characteristics require special material handling solutions. It is prone to producing high amounts of dust, which is easily combustible and a personnel risk. AZO’s engineering team carefully considers each of these factors to design a bulk fumed silica material handling system that ensures safe, reliable flow.
Fumed Silica Handling: Common Challenges

Proper handling and conditioning of fumed silica is necessary to prevent sticking and clogging.

Proper handling and conditioning of fumed silica is necessary to prevent sticking and clogging.

Manufacturers must contain fumed silica dust.

Manufacturers must contain fumed silica dust.
The high volumes of dust generated by fumed silica are an explosion risk. Explosion protection requires containment or venting to the outside of the facility. Every bulk ingredient handling system must incorporate explosion protection and dust mitigation equipment to protect an operation and its employees.

Bulk fumed silica handling requires space for explosion protection.

Bulk fumed silica handling requires space for explosion protection.
Any bulk ingredient handling operation must ensure adequate space for the installation of explosion protection and dust mitigation equipment. This may require some creativity in design and installation to ensure that necessary protection can fit into the available square footage — or be located in proximity to an exterior wall or roof — for venting. This can be especially challenging when adding explosion protection in an existing manufacturing plant.
Fumed Silica Handling Systems: Outcomes & Benefits
AZO’s experienced design engineers understand the unique properties of fumed silica. Every fumed silica bulk handling system we design incorporates equipment and solutions that reliably and effectively address the challenges outlined above. As a single-source provider of automated ingredient system equipment, AZO designs and engineers fumed silica handling solutions that enhance both safety and productivity in your facility.
With an AZO fumed silica handling system, your operation will:
- Avoid bridged or plugged equipment to prevent downtime.
- Safely contain dust to significantly reduce explosion risk and safeguard the health and well-being of employees.
- Aid material flow when emptying storage vessels or conveying to processing machines.
- Optimize uptime with equipment that is easy to clean and inspect.
Questions About Bulk Ingredient Handling?
AZO’s Fumed Silica Handling Systems: Equipment & Engineering Solutions
AZO has years of experience handling fumed silica using unique, engineering-centric designs. Your solution will match your unique requirements and be optimized for the safest, most reliable handling process. Each system AZO engineers for fumed silica handling includes: