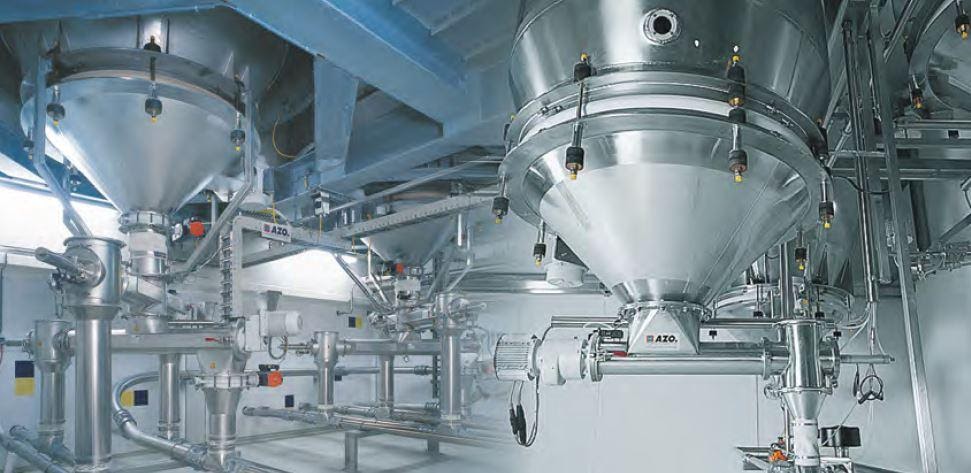
There are more than a few methods to induce flow when handling bulk material. We recently covered 3 unique and effective ways to get material moving, but there are much more worth exploring. As there are many different types of bulk material to handle, so too are there many methods to assist the flow of different types of materials.
What follows is three more pertinent methods that assist material flow, this time specifically grouped together by how they accomplish this task.
Material vibrators create vibratory motion where they are installed
As discharge aids, material vibrators directly create vibratory motion. Such motion excites the localized area wherever they're installed. Two different types of material vibrators are primarily used in the material handling world, electrically-driven material vibrators and pneumatically-driven material vibrators. Each has its benefits, which we cover in a free guide available on the AZO site.
Vibrating grids offer additional safety benefits on bag dump stations
Vibrating grids are used specifically on bag dump stations. As undesirable material being released into the product stream should be avoided, an appropriate opening size can be set for a vibration grid in order to keep material of a certain size out. Additionally, these grids aid in ensuring the safety of operators. With a vibrating grid in place, operators are protected to a greater degree from rotating equipment that may be installed below.
Some materials don't discharge on their own through static grids. When this occurs, vibratory grids can be an effective means to excite the material flow process. The advanced version of a vibrating grid is known as a “crown sieve.”
Utilizing a live bottom bin activator reduces rat holes and bridging
Live bottom bin activators dispel difficult or flow-resistant product from a hopper. The near-uniform fashion in which material is agitated through a storage vessel accomplishes FIFO (first-in-first-out capability). More importantly, rat holes and product bridging are greatly reduced or even eliminated. Most any live bottom bin activator will differ from an impactor or a large outlet with a multi-screw discharger by putting more energy into the actual product. Multi-screw dischargers are also often difficult to clean and maintain due to their amount of internal and rotating parts.
Vibrating bin bottoms are also particularly versatile because the amount of energy input into the product can be increased or decreased by varying the amplitude of the vibration. Bottoms with an inverted cone on the inside make sure, at the most critical point, that material is not compressed too quickly. This occurs whether discharge is through a screw feeder, rotary valve or some other type of discharge application.
Live bottom bin activators can aid many different industries handling unique materials — from bits and inclusions to milk powder blends as well as sugar to name a few. They can be specifically utilized on a variety of pieces of equipment. Bag dump stations as small as 500 diameters can be outfitted with them. Twelve-foot diameter storage silos can be outfitted with vibration bottoms as well. Though the entirety of a vessel such as a tall silo would vibrate, most of the silo would minimally experience the vibration. The discharge is primarily where such motion would be felt.
As pictured, vibration bottoms can be outfitted with motor-driven vibrators.
A new, free guide from AZO further elaborates on various mechanical devices that are used to apply energy into material in order to induce flow. “Flow and Functionality: Determining The Proper Discharge Aids For Your Bulk Material Handling Process” contains pertinent information about many machines that are often used in concert with each other (as well as flow agents) to overcome the friction between material and the wall of storage vessels.
If you find that you have any other conveying queries, you can always feel free to speak to an AZO specialist. We have more than seven decades of experience in handling raw materials and shaping ingredient automation along the way. Contact our sales team for any questions on how to help your plant and processes run smoothly.