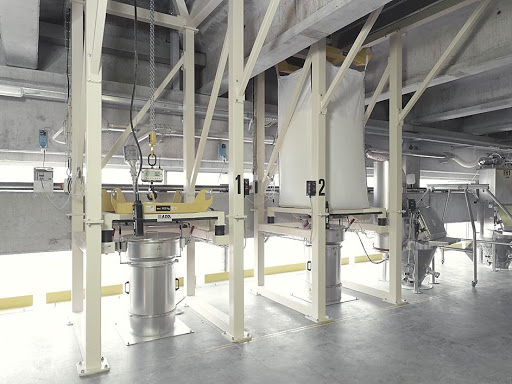
If you were asked to locate the most dangerous area for an operator to stand near a bulk bag unloader, where would you point? If you thought of the front side of the unloader, then you are correct. There are no safety brackets in this area. It’s required for space to be here so that the bag can be loaded in the first place, but this space also makes it possible for a bag to tip in the direction in the unlikely (but dangerous) event that the bag is not supported.
The front side of an AZO Model H Big Bag Unloader
Many bulk bag unloader manufacturers have a solution for supporting a bulk bag, but these solutions may not include a full support table. Some companies implement bars to hold bulk bags in place on an unloader. These bars may be welded in place, but in some cases they may be moveable (potentially allowing sliding during the time that they would be required to support a bag).
There are many features of a quality bulk bag unloader that help keep employees safe, but sturdy support for a bulk bag is so essential that it shouldn’t even truly be considered a “safety feature.” AZO and a few other ingredient automation manufacturers include support tables with their bulk bag unloader models as we believe a full support table is more comprehensive than simple bars. Certain support tables can also include some key additions that can ultimately assist with material flow, which we’ll also outline in this post.
Support tables support hanging bulk bags
A support table’s primary purpose is simply to hold the bulk bag in place. After bags have been hoisted upward and set in place on an unloader, the bags sit on these support tables. As hoisting a bag lifts 2,000 pounds upward of 20 feet into the air, it is not recommended under any circumstances that an operator should stand directly underneath the bag when transporting.
A modular big bag unloader with a “support table” (in red)
Still, in the event that an operator doesn’t take full advantage of a remote pendant to operate the bag hoist from a distance (as recommended), sturdy support tables more effectively offer a last line of defense than a group of support bars would.
A properly integrated bulk bag may not tip or fall very often at all, but it’s worth mentioning that the indirect costs of workplace injuries can amount to between four and 10 times the amount of direct medical costs. Reputational damage can also end up affecting morale and productivity in the long run for a company undergoing the effects of any workplace injury. Essentially, a support table is one element that can help prevent a bag from falling and injuring an operator (even if it’s not primarily built for safety purposes). The proper steps should still be taken to prevent workplace injuries at all times.
Additions to a support table assist material flow
There are also a couple of different choices for additions that can be equipped to specific support tables on big bag unloaders. These include material vibrators and bulk bag massagers. Both of these assist with dispensing material from the bag and are useful when working with poor-flowing products.
Material vibrators are located on the back of an unloader and shake the bag itself to help dispense the product. A bag massager is essentially an airbag that has a metal plate bolted at the top of it. An operator simply presses a button and three massagers move up in sequence to massage the bag. This effectively aids the flow of powder or material discharging outward.
As material is effectively discharged, less time is spent adjusting control settings to fix material flow. By including a support table in the design of a bulk bag unloader and equipping it with either a material vibrator or bulk bag massager, it is possible for a system to run consistently and efficiently (leaving your company to reap potential benefits).
For more tips on conveying certain materials or other topics related to the functions of robust bulk bag unloaders, contact an AZO sales representative or download our thorough bulk bag unloading buying guide. The AZO team has years of application experience to help you with your plant automation challenges.