Handling non-free flowing ingredients like TiO2 can be exceptionally difficult. Prone to sticking and clumping as well as clogging filters and conveyance lines, TiO2’s unique properties must be considered when selecting methods of material storage, conditioning, conveying, emptying, and dispensing.
TiO2 (Titanium Dioxide) Handling Solutions
Whether sticking to conveyor lines or resisting emptying from a bulk bag, TiO2’s characteristics require experienced design and engineering to optimize a bulk material handling system.
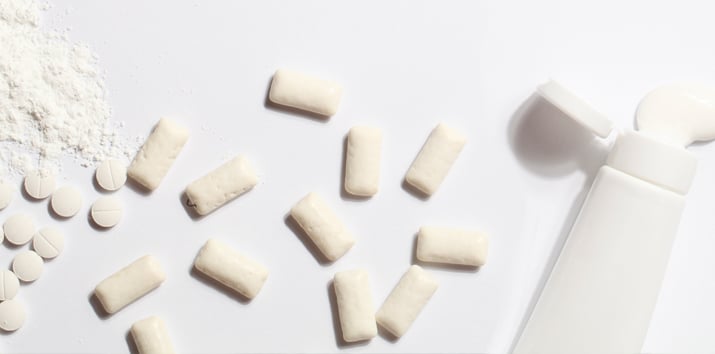
TiO2 Handling: Overview
Bright white and used in a variety of everyday products, TiO2 is an extremely common ingredient in many bulk ingredient handling operations, including personal products, poly and plastics, chemicals, and pharmaceuticals. Characterized by fine particles that flow poorly, TiO2 is moderately abrasive and forms heavy, dense clumps. These critical attributes can make emptying this ingredient out of storage vessels or successfully conveying it challenging. AZO’s engineering team carefully considers each of these factors to ensure the design of a TiO2 handling system is safe, reliable, and dust free.
TiO2 Handling: Common Challenges

Proper handling and conditioning of TiO2 is necessary to prevent sticking and clogging.

Proper handling and conditioning of TiO2 is necessary to prevent sticking and clogging.

Manufacturers must contain TiO2 dust.

Manufacturers must contain TiO2 dust.
With its fine particle size, TiO2 can produce a significant amount of dust. The high volumes of dust generated by handling TiO2 — if not properly contained or vented out of the facility — create an unsafe working environment for personnel. Every bulk TiO2 handling system must incorporate dust mitigation equipment to safeguard an operation and its employees.

Government regulation and accurate lot tracking are often required.

Government regulation and accurate lot tracking are often required.
Used as a color additive in the food, pharmaceuticals, and cosmetics industries, the U.S. Food and Drug Safety Administration (FDA) has assessed and approved the general safety of TiO2 in consumer products. Food safety includes two issues: unsafe chemicals that might be in the bulk TiO2 when delivered by the vendor; and general limits on the amount of TiO2 in any given product. FDA compliance failures such as inaccurate batching logs or documentation errors — mistakes that commonly occur with manual logging of batch history — significantly increase the risk of non-compliance fines.
TiO2 Handling Systems: Outcomes & Benefits
AZO’s experienced design engineers understand the unique properties of TiO2. Every TiO2 bulk handling system we design incorporates equipment and solutions that reliably and effectively address the challenges outlined above. As a single-source provider of automated ingredient system equipment, AZO designs and engineers TiO2 handling solutions that enhance both safety and productivity in your facility.
With an AZO TiO2 handling system, your operation will:
- Avoid plugged or clogged equipment to prevent downtime.
- Condition TiO2 effectively to promote smooth flow or discharge.
- Safely contain dust to safeguard the health and well-being of employees.
- Optimize uptime with equipment that is easy to clean and inspect.
Questions About Bulk Ingredient Handling?
AZO’s TiO2 Handling Systems: Equipment & Engineering Solutions
AZO has years of experience with TiO2 handling using unique, engineering-centric designs. Your solution will match your unique requirements and be optimized for the safest, most reliable handling process. AZO engineers use the following equipment for TiO2 handling: